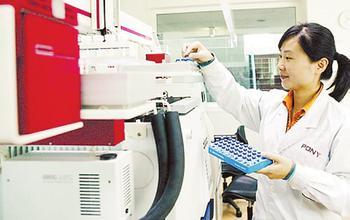
Testing approved by the purchaser
The pilot implementation of third-party testing was the biggest change in the implementation of fixed-point procurement for office furniture in 2012, and was also a new measure launched by the National Mining Center in 2012. If the purchase amount of the procurement unit is between RMB 500,000 and RMB 1,200,000, and the company is not sure of its quality, it may entrust the National Furniture and Indoor Environmental Quality Supervision and Inspection Center, which has signed a strategic cooperation agreement with the National Mining Center, to carry out testing and testing. It is borne by the National Mining Center.
Fang Ning said that when the State Office procured a batch of office furniture, it invited inspection agencies to carry out the whole process of inspection, including raw materials, production processes and finished products, and obtained good test results.
It is understood that when the Chinese Language Academy purchases a batch of furniture and invites the testing agency to carry out the finished product inspection before acceptance, it finds that the product is unqualified. All products are returned to the supplier for re-production, and all products pass the inspection at the time of re-inspection. Fang Ning said, “This is really a wake-up call to suppliers. In fixed-point purchases, some suppliers try to muddle through the borders. This dishonest attitude may cause suppliers to accumulate in the government procurement market. It is impossible to restore credibility to zero and it will not be able to establish a foothold in the government procurement market for a long time."
Testing indicators must be scientific and reasonable
It is understood that during the inspection process, some procurement agencies have proposed higher detection technology indicators. Some testing technical indicators have deviated from reality, and some are far higher than the national standards. If the testing requirements of individual units are too high, 95% of products on the market will not meet the requirements.
In this regard, the National Furniture and Indoor Environmental Quality Supervision and Inspection Center Director Luo Ji told reporters that the furniture commission inspection generally has three basis, one is the standard, including national standards and industry standards; the second is based on the provisions of the tender documents; third It is necessary to respond according to the bidding documents. If the bidding documents make a higher promise than the bidding documents, they need to be tested according to higher standards.
Fang Ning said that in 2013, it will further improve related systems and work for third-party testing in fixed-point procurement of furniture, and do a good job in product testing. Not only does it require suppliers to cooperate, but also the procurement organization should focus on the scientificity and rationality of the testing program.
Raw material testing is the key
According to reports, when the inspection agency commissioned by the National Mining Center provides inspection services for central ministries and commissions, it is divided into two types: one is the finished product sampling inspection before acceptance, and the other is the whole process inspection, which includes raw materials and semi-finished products in production. And finished product sampling.
Luo Hao said that the inspection should focus on two aspects. The first is raw materials, and it is necessary to determine whether the raw materials have not been replaced and whether the raw materials are filled with water. For example, if the request is particle board, whether the product provided has become a medium-density board, the thickness of the steel plate is required to reach 1.5mm, and whether the thickness is enough. Second, to verify whether the technical indicators meet the actual requirements. “Usually, if we can do a good job in testing raw materials before production, there will basically be no problems in the later period. Therefore, the detection of various raw materials is the most critical.â€
With the prolonged operation of the Steam Turbine power generation equipment, after a long period of start-stop operation, the loss of the equipment gradually increases, which inevitably causes the wear, tear, deformation and damage of equipment components, making the whole operation of the machine threatened by risky factors, and make the unit's operating efficiency significantly reduced, and hence affecting the economic performance of the unit. Therefore, the equipment maintenance is particularly important. However, many users do not have professional technical experience and staff, given that, QNP is dedicated to provide its customers with a full range of unit maintenance and repair services, as well as the upgrading of old units. At the same time, QNP also provide its customers with long-term training and debugging services. QNP can develop tailor-made maintenance program upon its customers requirements, provide direct one-on-one service, and realize life-long service to our users.
QNP provides maintenance, repair, overhaul and upgrade services and spare parts supply for turbine-generator set of 0-1000MW.
Power Plant Installation,Steam Turbine Care,Generator Care,Electrical Cabinet Care
Shandong Qingneng Power Co., Ltd. , http://www.qnpturbines.com