I. Introduction
In today’s metal processing industry, laser-cutting machines have become indispensable equipment because of their high efficiency, precision and adaptability. They utilize high-power density laser beams to cut and engrave multiple materials, playing an essential role in automotive, aerospace and precise mechanical manufacturing.
Furthermore, laser cutters ensure efficiency, product quality, and consistency, serving as one of the core cutting technologies in modern manufacturing.
However, despite the ever-advanced laser cutting technology, there are problems arising from time to time during the real operation course. For example, inaccurate focusing lenses may cause unsmooth edges, and unsteady laser power may cause inconsistent cutting speed and incomplete cutting of materials.
During cutting, these issues not only waste materials but also increase costs, delay delivery time, and even impact market competitiveness. Therefore, timely recognition and resolution of common problems in laser cutting is pivotal in ensuring smooth production procedures and improving product quality.
In this comprehensive guide, we'll explore the most common laser cutting machine problems, their causes, and effective troubleshooting methods. We'll also delve into preventive maintenance strategies and best practices to help you keep your laser cutter operating at peak performance. By the end of this article, you'll be equipped with the knowledge to identify, resolve, and prevent a wide range of laser cutting machine issues, ensuring smoother operations and superior results in your projects.
II. Understanding Laser Cutting Machines
1. Basic Components
A laser cutter’s basic components incorporate a laser generator, a cutting head, a control system, a transmission system(optical system), an assist system and a cooling system. These components interact with each other to precisely control the position and movement of laser beams and then to finish the precise cutting of materials.
(1) Laser generator:
As the core component, the laser generator generates laser beams.
(2) Cutting head:
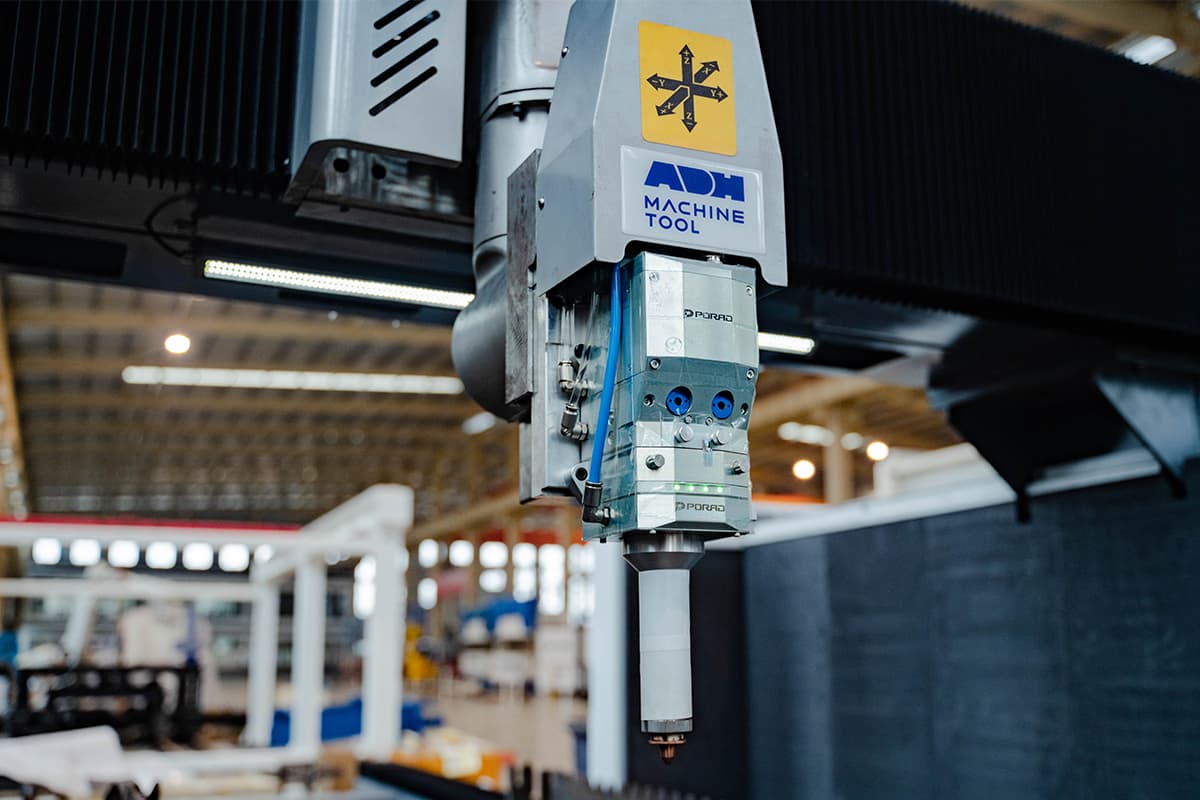
It contains focusing lenses and nozzles to concentrate laser beams and lead assist gases to cutting areas.
(3) Control system:
As the brain of a laser cutting machine, the control system controls the machine’s movement and laser emission and ensures accurate cutting.
(4) Transmission system(optical system):
For CO2 laser cutting machines, laser beams will be led to the cutting head through reflective mirrors and for fiber laser cutting machines, they will be transmitted by fiber optic cables.
(5) Assist gas:
Assist gases are used to blow the melt and clean the cutting areas so as to smooth the cutting course.
(6) Cooling system:
Usually, it’s the chiller unit to cool the laser generator and other components so as to keep the machine’s steady operation.
The interaction of these components finishes the precise cutting through the accurate adjustment of laser power, cutting speed, focusing, and pressure of assisting gases.
2. How They Interact with Each Other
Let‘s view a short video to learn its working processes first:
How they interact with each other? What’s the procedure of the laser cutting? Here is step by step introduction of a laser cutting machine’s working procedures.
(1) Step one: laser generation
As core components, lasers generate laser beams. Lasers excited by electricity or other light sources generate work substances, such as CO2 or fiber. Laser beams possess high levels of monochromaticity, directionality, and brightness.
(2) Step two: laser transmission
Generated laser beams will be concentrated into a small light spot through a series of optical systems, including reflective mirrors and focusing lenses. As for CO2 laser cutting machines, laser beams will be transmitted by reflective mirrors. While in fiber laser cutting machines, lasers will be transmitted on the cutting head directly through fiber cables.
(3) Step three: Focus and material processing
Laser beams will be concentrated in a small spot with extremely high-density laser power, which can heat the material into evaporation points. During the course, the material will be melted, evaporated or burned to the ignition point and form a small hole. With the relative movement of the cutting head, the small hole will be lined as a narrow silt according to the cutting direction of the cutting head.
(4) Step Four: Assist gas
During cutting, the cutting head will inject assist gases, such as oxygen, nitrogen and air, which can not only blow the melt off and keep the cut clean but also participate in a chemical reaction. In oxygen cutting, for instance, oxygen reacts with hot metal to generate more heat, accelerating the cutting process.
(5) Step Five: Control system
The CNC control system controls the whole cutting process. Users can design the moving path of the cutting head and parameters through the program, such as laser power, cutting speed and focal length, which enables laser cutters to cut intricate patterns with high accuracy.
All the components and working principles of a laser cutter ensure its high efficiency and accuracy in industrial production and make it a pivotal machine, no matter whether it is in metal and non-metal processing.
3. Mainstream Types of Laser Cutting Machines
There are two mainstream types of laser cutting machines: CO2 laser cutting machines and fiber laser cutting machines.
(1) CO2 laser cutters
CO2 laser cutting machines utilize gas as a laser which is produced in electrical discharges by mixing CO2 gas with other gases (such as nitrogen and helium). With a wavelength of 10.6 micrometres, they are suitable for non-metal cutting, such as wood, plastic, fabric and acrylic.
High-power CO2 laser cutting machines can also cut metals. Basically, CO2 laser cutters can produce smooth and clean cutting surfaces with high verticality, suiting materials with high requirements for cutting accuracy.
(2) Fiber laser cutters
Fiber laser cutting machines use solid lasers generated by mixing fiber cables. With a wavelength of 1.06 micrometers, fiber laser cutters possess higher electricity-light transformation rates, lower energy consumption and better laser beams.
With a compact structure and free from maintenance, they are suitable for cutting high-reflective and conductor-grade metal materials. Due to their high speed and efficiency and low absorption rate, fiber laser cutters are mainly used for metal processing.
(3) Typical applications and materials:
CO2 laser cutting machines are suitable for non-metal cutting, such as wood, plastic, fabric, acrylic, and other high-accuracy metal cutting.
Fibre laser cutting machines are mainly used for metal cutting, such as steel, copper, and aluminium, and are especially applied for metal sheet processing.
III. Common Problems in Laser Cutting Machines
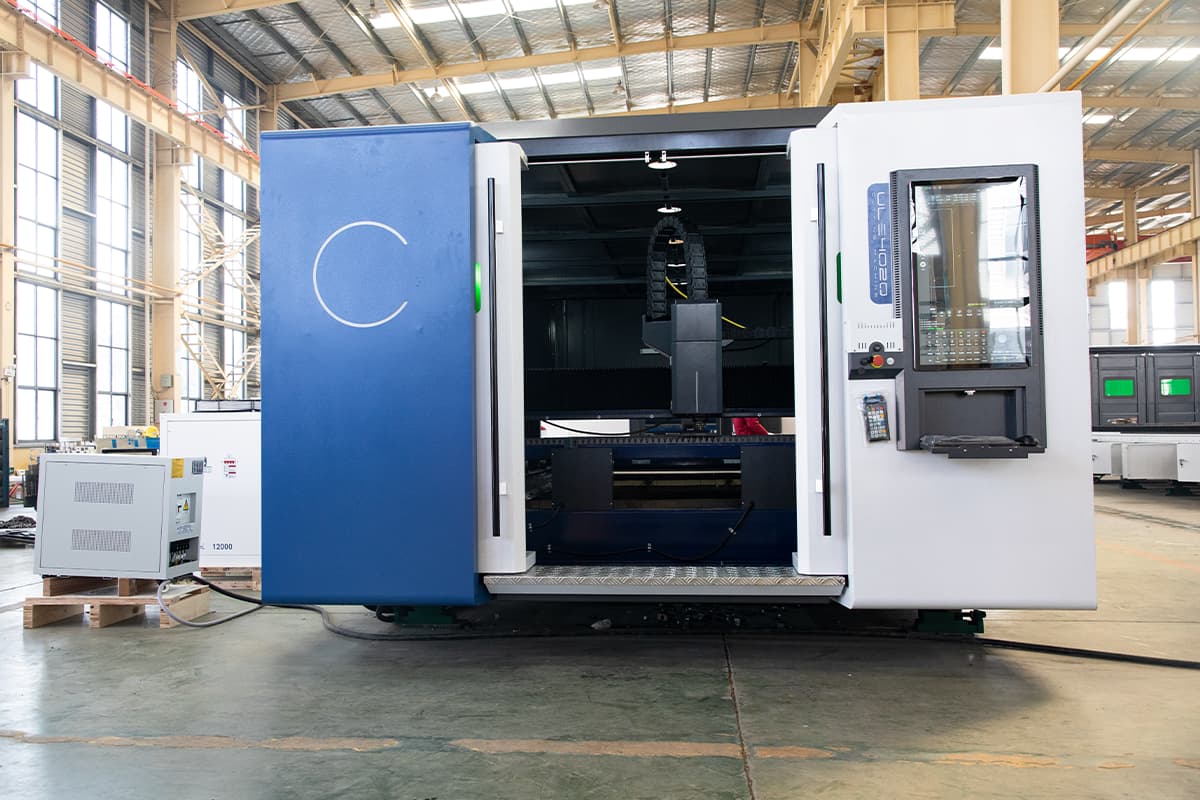
Although laser cutting machines are widely used in various sectors by virtue of high efficiency and precision, they may break down at times while running due to many factors such as materials, technology and software.
In the following chapter, common problems and solutions will be dicussed in detail interms of material-related issues, technical difficulties and software and control system errors.
1. Material Issues
Problems caused by using inappropriate materials (reflectivity, thickness). During the laser cutting, the selection of materials matters. Inappropriate materials will lead to over-high reflective rates and improper thickness, impacting cutting quality.
(1) Reflective Material Issue
High-reflective materials, such as copper and aluminum alloy, may cause laser reflection to damage the cutting machine or impact cutting quality. Therefore, the solution is to use specialized laser-absorbing materials or adjust the parameters, such as lowering laser power and increasing assist gas pressure.
(2) Material Thickness Issue
Laser-cutting machines have certain requirements for the material thickness. Too thin or too thick materials will impact the cutting effect. For example, materials that are too thin entail lower laser power so as to avoid burning through materials.
(3) Poor Material Compatibility
Using materials that are not compatible with laser cutting can lead to poor cut quality and potential damage to the machine. Some materials may produce excessive smoke, fumes, or residue that can contaminate the laser optics and other components. It is crucial to use materials that are specifically recommended for laser cutting and to follow any material-specific guidelines provided by the manufacturer.
(4) Contaminated Materials
Materials that are dirty, oily, or coated with residue can negatively impact the cutting process. Contaminated materials can produce inconsistent cuts and may cause the laser beam to scatter or weaken. Proper cleaning and preparation of materials before cutting are essential to ensure optimal performance. Cleaning methods can include using a soft brush, paper towels, and appropriate solvents like isopropyl alcohol or vinegar to remove any surface contaminants.
2. Alignment Problems
(1) Misaligned Laser Beam
A misaligned laser beam is another common issue that affects the precision and accuracy of cuts. Misalignment can occur due to physical impacts, vibrations, or gradual shifts over time. Symptoms of a misaligned beam include uneven cutting depths and inconsistent cut lines. Regular alignment checks and adjustments are essential to maintain the laser's accuracy.
(2) Beam Divergence
Beam divergence occurs when the laser beam spreads out over a distance, reducing its cutting power and precision. This problem is often due to issues with the laser optics or mirrors. Ensuring that all optical components are clean, properly aligned, and in good condition can help reduce beam divergence and improve cutting performance.
3. Software and Control System Errors
(1) Software Glitches
Software glitches can disrupt the operation of laser cutting machines, leading to errors in the cutting process. These glitches can be due to outdated software, bugs, or conflicts with other software. Regular updates and maintenance of the machine's software can help prevent these issues. For example, ensuring that the software settings are correct for the material being cut and updating the software to the latest version can mitigate many problems.
(2) Control Panel Failures
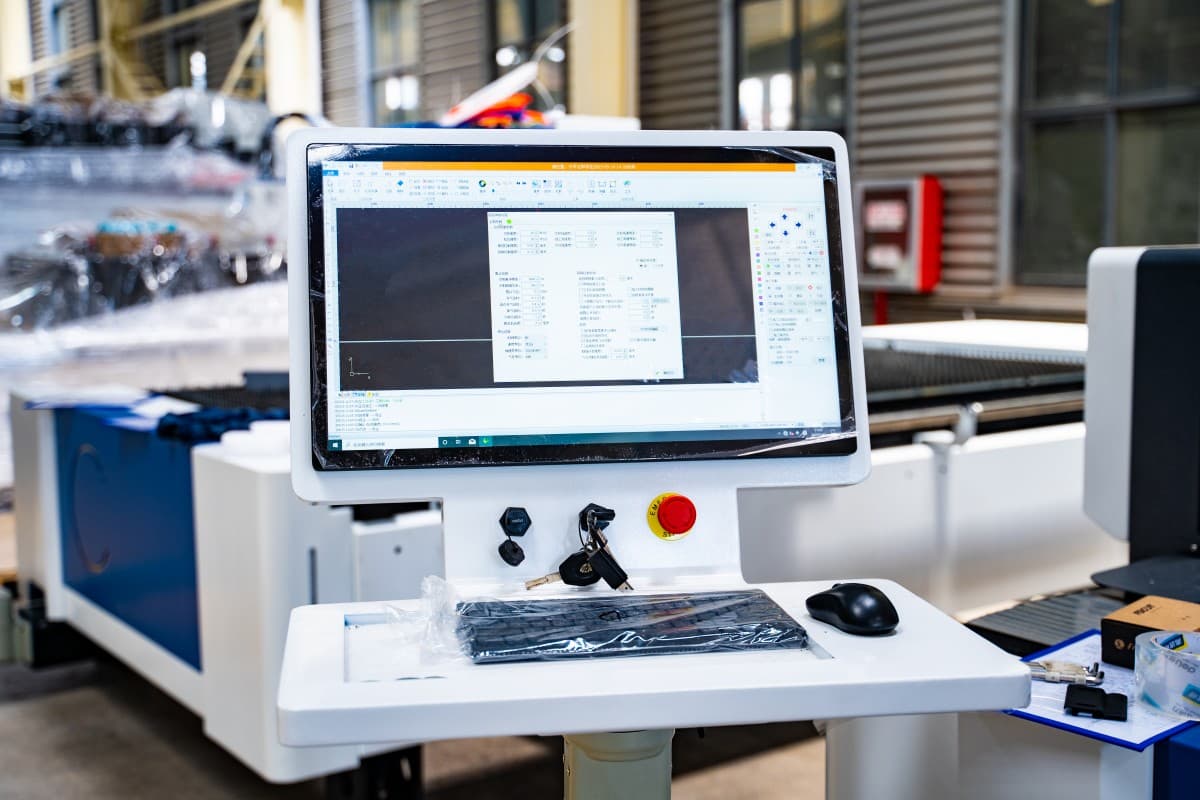
Failures in the control panel can make it difficult to operate the machine effectively. These failures may manifest as unresponsive buttons, incorrect settings, or complete system shutdowns. Regular inspection and maintenance of the control panel, along with prompt troubleshooting of any issues, are important to ensure smooth operation.
4. Power Issues
(1) Inconsistent Power Output
One of the most frequent problems encountered with laser cutting machines is inconsistent power output. This can lead to uneven cuts, which compromise the quality of the finished product. Inconsistent power output may be caused by several factors, including fluctuations in the power supply, issues with the laser tube, or problems with the power control system. Regular calibration and monitoring of the power output can help mitigate this issue.
(2) Sudden Power Drops
Sudden power drops during operation can be particularly disruptive, leading to incomplete cuts and potential damage to the material being processed. These power drops can stem from electrical supply issues, faulty wiring, or degraded components within the machine. Ensuring a stable power supply and regular inspection of electrical connections can help prevent this problem.
5. Inconsistent Cutting Quality
(1) Uneven edges: The cut edges may appear rough or jagged instead of smooth and clean.
(2) Incomplete cuts: The laser fails to cut entirely through the material, leaving partially cut sections.
(3) Burning or melting of materials: Excessive heat can cause unwanted charring or melting, especially on heat-sensitive materials.
6. Focus and Lens Issues
(1) Improper focal length: The distance between the lens and the material is incorrect, resulting in unfocused cuts.
(2) Dirty or damaged lenses: Accumulated debris or scratches on the lens can distort the laser beam, affecting cut quality.
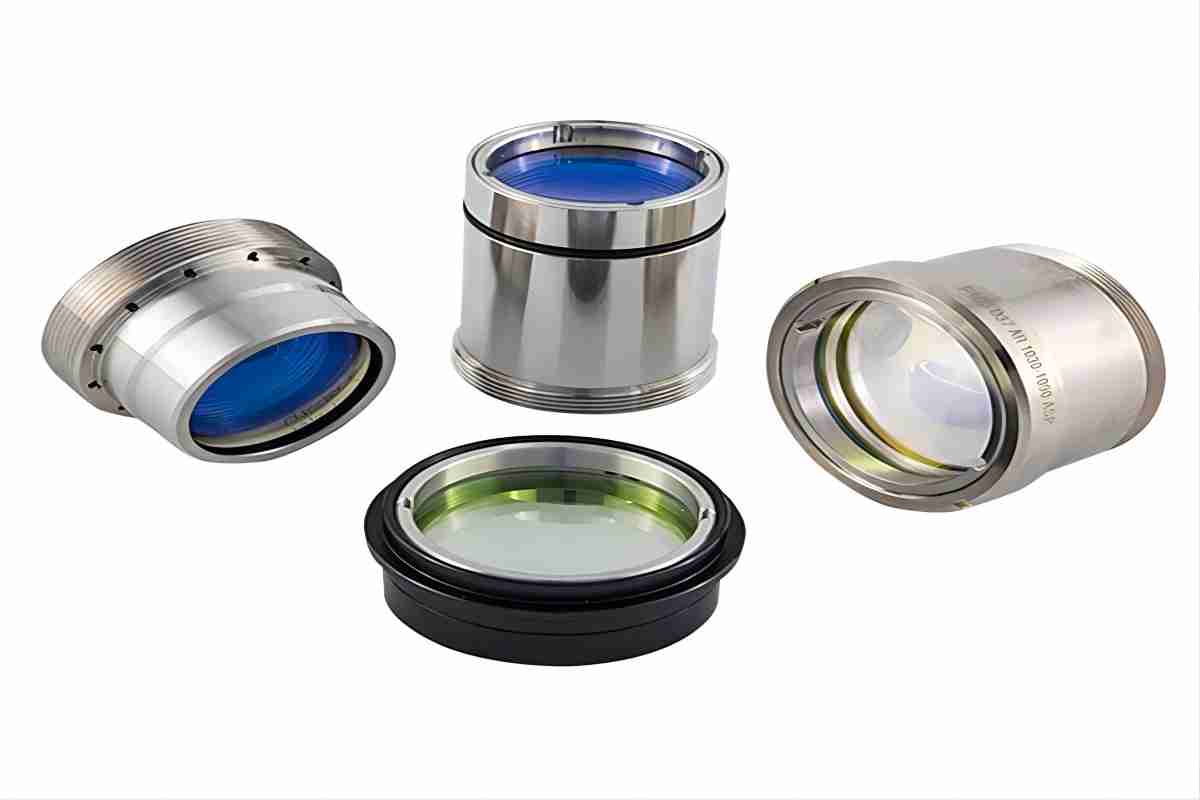
IV. Causes of Laser Cutting Machine Problems
1. Machine Maintenance Issues
- Lack of regular cleaning: Over time, dust, debris, and residue from cut materials can accumulate on various parts of the machine, including optics, mirrors, and the cutting bed. This buildup can interfere with the laser beam's path and affect cutting quality.
- Neglected component replacements: Laser cutting machines have several components that wear out over time, such as focus lenses, nozzles, and filters. Failing to replace these parts at recommended intervals can lead to decreased performance and various cutting problems.
2. Incorrect Machine Settings
- Improper speed and power settings: Each material and thickness requires specific laser power and cutting speed settings. Using incorrect settings can result in incomplete cuts, burning, or poor edge quality.
- Incorrect focal point: The focal point of the laser beam must be accurately set based on the material thickness. An incorrect focal point can lead to unfocused cuts and reduced cutting efficiency.
3. Environmental Factors
- Temperature fluctuations: Laser cutting machines are sensitive to temperature changes. Fluctuations can affect the laser's performance and the material's behavior during cutting.
- Dust and debris accumulation: A dusty or dirty environment can lead to rapid buildup on machine components, affecting cutting quality and potentially damaging sensitive parts.
4. Operator Error
- Lack of training or experience: Inexperienced operators may not recognize early signs of problems or may incorrectly set up the machine for different materials and projects.
- Incorrect material handling: Improper loading of materials, failure to secure them adequately, or using warped or damaged materials can all lead to cutting issues.
V. Detailed Troubleshooting Steps
1. Power Supply Troubleshooting
(1) Checking and Calibrating Power Output
To address inconsistent power output, start by checking the power supply to ensure it is stable and within the required specifications for your laser cutting machine. Use a multimeter to measure the voltage and current at various points in the system. If discrepancies are found, recalibrate the power supply according to the manufacturer’s guidelines. Additionally, inspect the laser tube for signs of wear and tear, as a degraded tube can affect power output.
(2) Inspecting Electrical Connections
Electrical connections should be regularly inspected for any signs of wear, corrosion, or loose connections. Loose or corroded connections can cause power drops and inconsistent performance. Tighten any loose connections and clean any corrosion with a suitable cleaner. Replace any damaged wires or connectors to ensure a reliable electrical path.
2. Beam Alignment Techniques
(1) Step-by-Step Realignment Procedures
- Turn off the machine and allow it to cool down if necessary.
- Access the laser path and identify the mirrors and lenses.
- Clean all optical components using a recommended lens cleaner and lint-free cloth.
- Use an alignment tool or laser alignment card to check the laser path.
- Adjust the mirrors incrementally to ensure the laser beam is centered and aligned at each mirror and lens.
- Test the alignment by making a test cut on a piece of scrap material and check for uniformity.
(2) Using Alignment Tools
Using specialized alignment tools can make the process more precise and efficient. Tools like laser alignment kits, alignment cards, and beam combiners can help you achieve accurate alignment. Follow the tool manufacturer’s instructions for best results.
3. Material Handling and Preparation
(1) Ensuring Clean and Compatible Materials
Always use materials that are clean and free of contaminants. Wipe down the materials with a dry or slightly damp cloth to remove dust and debris. Ensure the materials are compatible with laser cutting by consulting the machine’s user manual or material compatibility charts provided by the manufacturer.
(2) Proper Material Loading Techniques
When loading materials onto the laser cutting bed, ensure they are properly secured and flat. Any warping or uneven surfaces can affect the cutting accuracy. Use clamps or weights if necessary to keep the material in place. Additionally, make sure the material is positioned correctly according to the cutting design.
4. Software and Control Solutions
(1) Updating and Reinstalling Software
Regular software updates are essential to keep your laser cutting machine running smoothly. Check for updates from the manufacturer and install them promptly. If the software is causing issues, consider reinstalling it to resolve any glitches. Always back up your settings and configurations before performing updates or reinstallations.
(2) Resetting and Configuring Control Panels
If the control panel is unresponsive or malfunctioning, try resetting it to the factory settings. Refer to the user manual for the reset procedure. After resetting, reconfigure the control panel settings according to your cutting requirements. If problems persist, it may be necessary to replace the control panel or consult the manufacturer for further assistance.
5. Addressing Cutting Quality Problems
(1) Adjusting speed and power settings
Experiment with different combinations of cutting speed and laser power. Start with the manufacturer's recommended settings for your specific material and adjust as needed.
(2) Cleaning and aligning optics
Carefully clean all mirrors and lenses using appropriate cleaning solutions and techniques. Check and adjust the alignment of mirrors to ensure the laser beam travels the correct path.
6. Dealing with Focus and Lens Issues
(1) Cleaning and replacing lenses
Regularly clean the focus lens using appropriate cleaning solutions and techniques. If a lens is damaged or heavily worn, replace it according to the manufacturer's recommendations.
(2) Adjusting focal length
Verify that the focal length is correctly set for the material thickness you're cutting. Most machines have a way to adjust the focal point, either manually or automatically.
VI. Preventative Measures
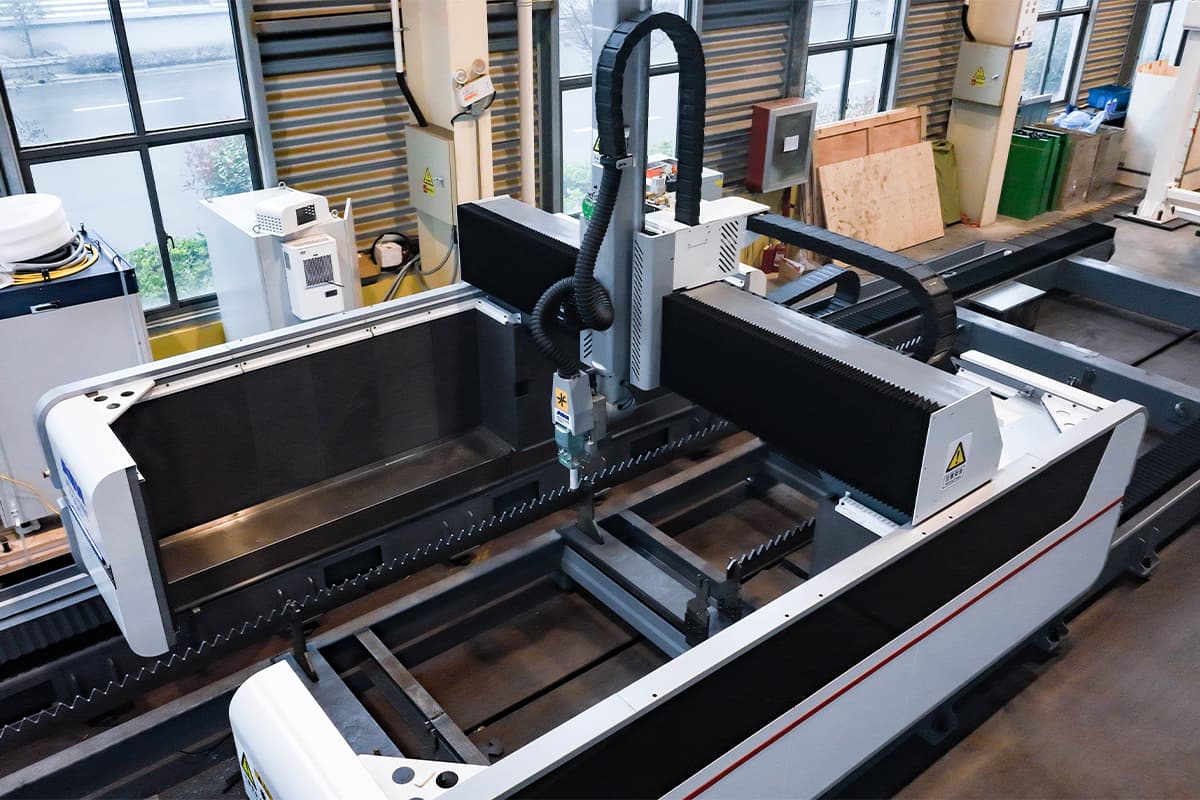
Preventive maintenance is crucial for the efficient operation of laser cutting machines. Preparing and implementing a maintenance plan can significantly reduce machine breakdowns and prolong machine lifespan. The following are some essential preventive strategies.
1. Regular Maintenance Schedules
Implementing a regular maintenance schedule is crucial for ensuring the longevity and optimal performance of your laser cutting machine. A well-maintained machine is less likely to experience unexpected breakdowns and will consistently produce high-quality cuts. Maintenance tasks should be performed on a daily, weekly, and monthly basis, depending on the machine's usage and the manufacturer's recommendations.
(1) Daily Maintenance Tasks:
- Clean the laser cutting bed and remove any debris.
- Check and clean the laser lens and mirrors.
- Inspect the cooling system and ensure it is functioning properly.
- Verify that all safety features are operational.
(2) Weekly Maintenance Tasks:
- Inspect and tighten any loose mechanical components.
- Check the alignment of the laser beam.
- Lubricate moving parts as recommended by the manufacturer.
- Perform a thorough inspection of the electrical connections.
(3) Monthly Maintenance Tasks:
- Conduct a detailed inspection of the laser tube for signs of wear.
- Test the machine's calibration and make necessary adjustments.
- Review and update the machine's software if needed.
- Clean and inspect the exhaust system to ensure proper ventilation.
2. Routine Inspections and Cleanings
Regular inspections and cleanings are essential for preventing issues before they become serious problems. Operators should develop a checklist to ensure that all critical components are inspected regularly. Key areas to focus on include:
- Laser Optics: Ensure lenses and mirrors are free from dust, smoke residue, and other contaminants.
- Cooling System: Check for leaks, ensure coolant levels are adequate, and inspect hoses for wear.
- Exhaust System: Clean filters and ducts to maintain proper airflow and remove any blockages.
- Mechanical Components: Inspect belts, pulleys, and gears for signs of wear and replace as necessary.
3. Training and Best Practices for Operators
Proper training and adherence to best practices are vital for the safe and efficient operation of laser cutting machines. Operators should receive comprehensive training on machine operation, safety protocols, and troubleshooting techniques. Regular refresher courses can help keep operators up-to-date with the latest advancements and best practices.
Best Practices:
- Always follow the manufacturer's guidelines for operation and maintenance.
- Use personal protective equipment (PPE) such as safety glasses and gloves.
- Keep the work area clean and free of flammable materials.
- Avoid unauthorized modifications to the machine.
- Document and report any issues or irregularities promptly.
By implementing these preventative measures, operators can significantly reduce the likelihood of machine failures and extend the operational life of their laser cutting equipment.
VII. Advanced Troubleshooting Techniques
As machines for precise processing, they may have many problems in operation. Advanced troubleshooting techniques can help operators find out problems and reasons so as to take effective methods .
1. Diagnostic Tools
Diagnostic tools for laser cutting machines mainly incorporate multipurpose testing instruments, specialized software and built-in self-diagnostic systems, which can test the core paraments of laser powers, optical path alignment and electrical systems. I will introduce the three diagnostic tools in detail.
(1) Multipurpose testing instruments
Multipurpose testing instruments, such as Laser power meters and multifunctional electric meters, are mainly used to measure laser output power and electrical connection status.
(2) Specialized software
Many laser cutting machines are equipped with specialized diagnosis software that can test the machine comprehensively, including software errors and hardware failure through a computer connection.
(3) Built-in self-diagnostic systems
Modern laser cutting machines are normally equipped with a self-diagnostic system that can carry out self-diagnosis and report fault codes to locate problems rapidly.
2. How to Use Them
We should set basic settings for diagnostic tools according to the operation manual or manufacturers’ instructions. Then, choose proper diagnostic tools based on encountered problems to have a test. For instance, if a laser cutting machine doesn’t perform well, a laser power output meter should be used to test if the output power is fine.
(1) Case one:
The intermittent cutting phenomenon occurs as a laser cutter in the cutting process. Using multipurpose electric meters can detect loosened electricity source connections. So, after fastening the connections, the problem is solved.
(2) Case two:
The decreasing accuracy of a laser cutting machine can be analyzed by specialized software. After testing, the optical paths are adjusted according to software instructions. As a result, the cutting accuracy is restored.
3. When to Call a Professional
Although many problems can be solved by the methods above, sometimes, we need to turn to professionals for help:
(1) Scenarios where professional help is necessary
Intricate hardware failures: such as laser damage, main control board malfunctions. These problems should be solved by professionals with professional knowledge and tools.
Repetitive issues: if a problem occurs repetitively, there may be more serious failures, which require technicians to have thorough diagnoses.
(2) How to choose the right service provider
When choosing the service provider, many factors should be considered:
Professional Qualifications: service providers with official certifications and good reputations should be chosen.
Service experiences: understanding the experience and cases of service providers in laser cutting machine maintenance is important.
Response time and service quality: choose providers who can respond quickly and offer high-quality services.
VIII. FAQs
1. What causes inconsistent laser power output?
Inconsistent laser power output can be caused by several factors, including fluctuations in the power supply, issues with the laser tube, and problems with the power control system. Regular calibration and monitoring of the power supply, along with inspecting and maintaining the laser tube, can help mitigate these issues.
2. What materials should you avoid using with laser cutters?
Avoid using highly reflective materials, produce toxic fumes when cut, or are not compatible with laser cutting. Examples include PVC, ABS plastic, and certain metals. Always consult the machine’s user manual or material compatibility charts the manufacturer provides.
3. How often should you perform maintenance on your laser cutter?
Maintenance frequency depends on the machine's usage and the manufacturer's recommendations. Generally, daily, weekly, and monthly maintenance tasks should be performed to ensure optimal performance. Daily tasks include cleaning the cutting bed and optics, while weekly and monthly tasks involve more thorough inspections and calibrations.
IX. Conclusion
In the article, the common failures and issues of laser cutting machines are explained in detail so as to serve as a reference for enterprises and individual hobbyists. In addition, an important factor you should notice is the selection of the right service providers. A service provider can reduce the repair and maintenance costs of a laser cutting machine and prolong its lifespan which can maximize the benefits for your companies or businesses.
Customized fiber laser cutting solutions at affordable prices provided by ADH Machine Tool, from entry-level to high-end machines. For more specific configurations check our laser cutting machines for sale.
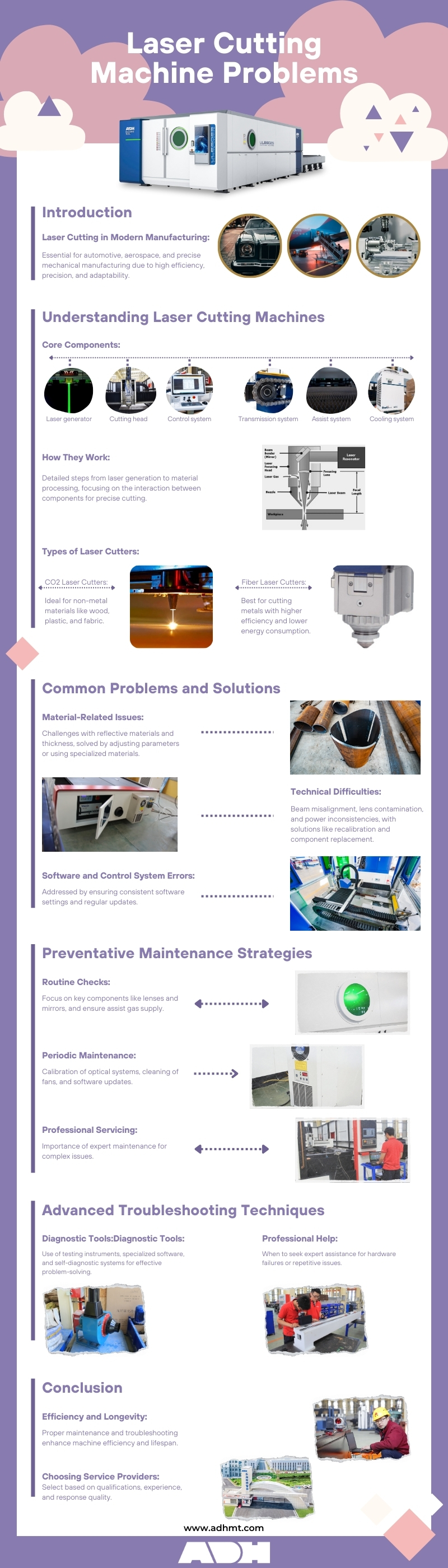
Download the Infographic With High Resolution
Angular Travel Electric Actuator,Angular Displacement Electric Actuator,Aluminum Alloy Sealed Electric Actuator,Reversible Ac Motor Angular Electric Actuator
NINGBO JIECHENG ELECTROMECHANICAL CO.,LTD. , https://www.jiechengmechanical.com