Servo Drive Computer Control System CNC Control Software
First, the composition of the computer numerical control system and the function of each part
For CNC machine tools, the control content mainly includes:
(1) Function control: Automatically read in the control information, so that the CNC system establishes the corresponding working status, thereby controlling the machine tool to perform corresponding actions. Such as lubrication, coolant supply, spindle motor on and off, speed, and coordinate axis function control.
(3) Signal processing: Analyze and process the status signal obtained during system operation and output the corresponding result. Such as: tool in place signal, workbench overtravel signal, and other detection signal input processing. Once the system gets these signals, the system will send out corresponding actions, such as the table overtravel protector alarm.
For the requirements of machine tool control functions, the computer numerical control system has corresponding function modules, and its composition principle is shown in Figure 4-1.
1. Input/Output Device Input Device: It is mainly used to input programs and data. Commonly used input devices: keyboards, optoelectronic input devices.
Output device: It is mainly used to provide various information and data to operators so that they can understand the control process in a timely manner. Commonly used output devices: Computer Numerical Control (CNC) devices such as printers, recorders, digital displays, CRT monitors, and paper tape punchers. It is a special-purpose computer that uses a stored program and is mainly used for numerical values ​​and Logical operations, real-time control of the machine. It consists of CPU, memory, input and output interface circuits and other components.
Printer Recorder Digital Display CRT Monitor
3. Function of servo drive and position detection device: receiving the feed speed and displacement command signal from the CNC device, after being converted and amplified by the servo drive circuit (such as the speed control unit), the servo drive device (if using a DC servo motor) , Drive the table movement of the machine tool, at the same time by the displacement sensor to detect the actual position of the actuator, and feedback to the CNC device, to achieve closed-loop drive, so that the position of the machine tool feeding parts speed is accurately controlled.
4. Auxiliary function drive circuit This part realizes the information transmission and transformation of the CNC device and the machine power. Its role is to receive CNC signals, and the machine is used to control the spindle, lubrication, cooling, tool change and other motor operations and other auxiliary functions. In addition, some status information of the machine tool is transformed and sent to the CNC device, such as: tool in place, workbench overtravel, etc. In the high-end numerical control system, the control work of this part is completed by the "built-in type" programmable controller (PC) subordinate to the CNC device, or by the "universal" programmable controller independent of the CNC device ( PC) to complete.
5. CNC System Software The working process of the CNC system supports the entire process of the software with the support of the hardware. Part or all of the CNC functions are implemented by software.
Figure 4-2 is a schematic diagram of the Fujitsu CNC system. This system is a microcomputer CNC system, and the principle of the CNC system can be further understood through this schematic.
Microprocessor: M6800, 8-bit microprocessor. ROM storage control program, RAM storage intermediate data and user processing program, with input / output interface connected with the machine operator panel, tape reader, hand pulse generator, machine controller, DC servo motor drive, pulse encoder disk detection Displacement achieves position feedback. Large-scale integration (LSI) circuits implement interpolation operations and have a high speed of operation.
Second, the main features of the CNC system
The main features of the CNC system are the following five points.
1. The system is flexible and variable, easy to change and expand, and versatility is the most prominent feature of the CNC system. Unlike the hardware CNC, once a certain model and function are formed, it cannot be changed at will, because the connection between hardware is dependent on the The wiring is implemented. For the CNC system, as long as the structure of the software is changed, new functions can be added and developed at any time to adapt to different requirements.
2. Easy to implement multi-function Because the computer has a rich instruction system and can perform complex calculations, it is much more convenient to implement multi-function and high-complexity control than to use a hardware system. For example, high-order curve interpolation, tool radius compensation, multi-coordinated linkage control, and some CNC systems can also perform numerical control programming during control processing, which is not possible in hardware systems.
3. High system reliability In the hardware control system, the machining program is entered one by one by the reader, but the CNC system can input the machining program once into the memory, which can reduce input failures. Since the CNC system hardware is much less than the NC system, the error rate of the system components is also relatively reduced, making the system work stable and reliable. Because the functions of the CNC system are all realized by software, as long as the software is perfect, it will not be possible to generate software running errors in the continuous system work in the future. Therefore, the continuous failure-free time of the CNC system can reach tens of thousands of hours.
4. Easy maintenance Because the CNC system has strong functions, the system function is modular, and software fault diagnosis is used to make the CNC easy to repair.
5. The communication function of the CNC system With the development of manufacturing technology, the CNC system can be controlled centrally. This function is indispensable. For example, in DNC, FMS, and CIMS systems, communication between systems is required.
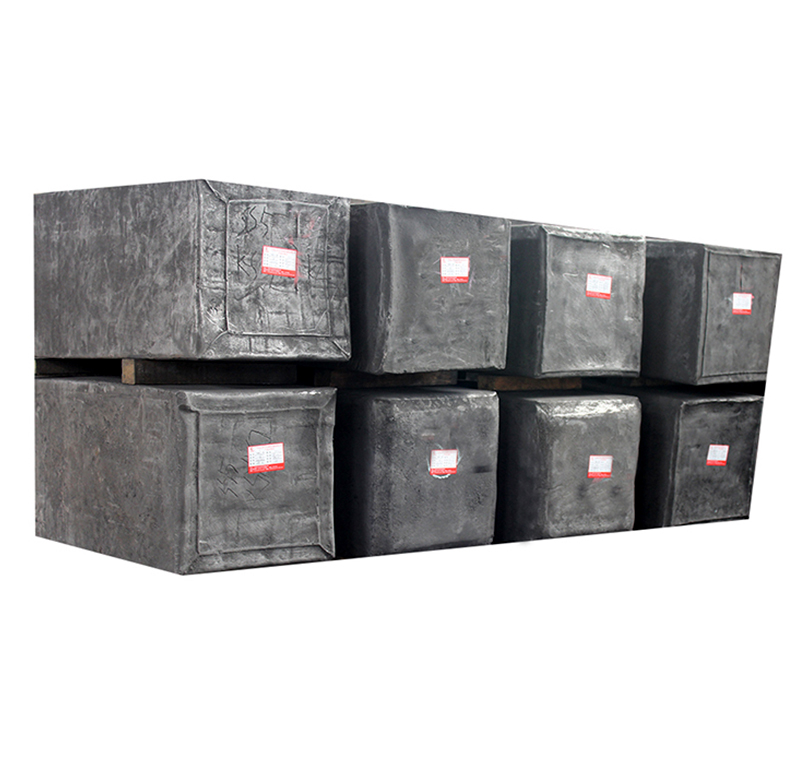
Our isostatic graphite and Molded Graphite were tested at the National Electrical Carbon Products Quality Supervision and Inspection Center. The main physical and chemical performance index as follows: the compressive strength--125 mpa, shore hardness -- 65 degrees, resistivity --12 mu Ω m. At the same time, the 10μm,8μm,6μm,4μm products have already began Large-scale production,.and unanimously acknowledged by customers. The 2μm,1μm graphite products are under trial. Our company high quality of isostatic pressing special graphite yield above 90%, far ahead of industry the yield of 70%, the first in the country.
Company main products:
2.Molded graphite block
3.Graphite rod
4.Graphite tube
5.Graphite plate
7.Graphite crucible
Customized High Pure and density graphite products/graphite block for EDM
Edm Graphite,Graphite Block For Edm,Edm Graphite Electrodes,Isostatic Graphite Column
CARBONS TECH&CREATION(HENAN) INDUSTRY CO.,LTD , https://www.carbongraphitepart.com