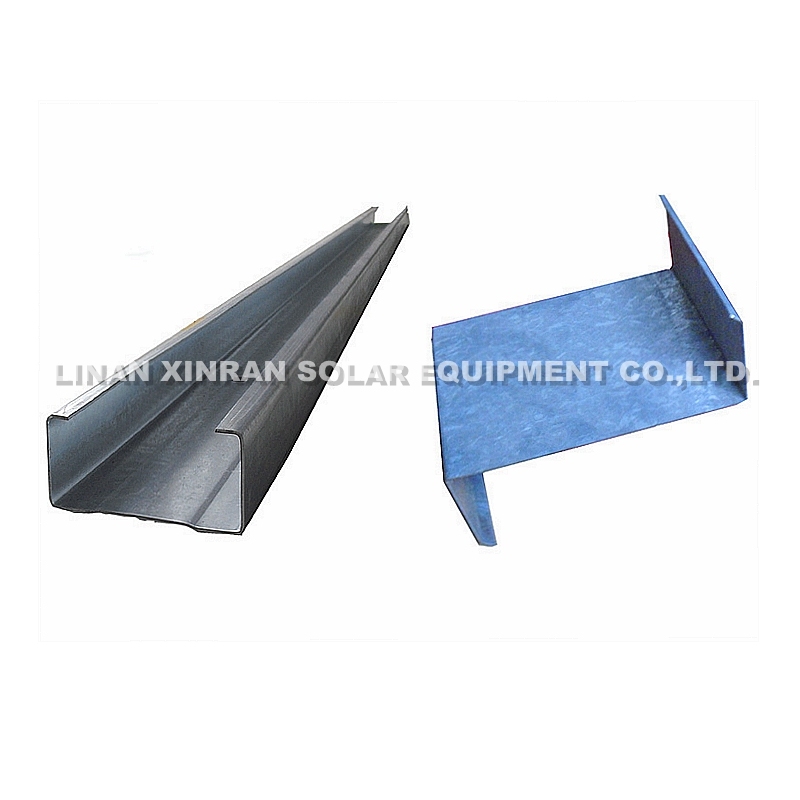

(1)The main technical parameter
1.Rolling product specification:width 100mm~300mm,high 40mm~80mm,thickness2.0mm~3.0mm
2.The speed of rolling:12-15 m/min
3.Number of sets of molding:17 sets main roller
4.Number of sets of leveling: 7 sets leveling roller
5.Transform line:2 sets
6.Installation form:Adopt arch type
7.Roller type: use split type
8.Roll material: GCr15 quenching treatment, HRC58-62
9.Spindle material: 45 quality steel quenched and tempered
10.main motor power:15KW
11.Hydraulic station motor power:7.5KW
12.Change the specifications speed: a full set of 10 minutes
13.The method of Cutting and punching:After forming then punching and finally cutting
14.The material of cutting knife and punching mold:Cr12 quenching treatment.
15.Electronic control system:The whole machine use  industrial computer PLC Siemens frequency conversion to control.
16.Main machine size:length 11m×width 2.3m×high 1.6m (including main motor)
17.Total weight of equipment:Around 12000kg
(2)Composition of equipment:
1.Guide
To prevent the plate move in production process to keep the product quality.
2.leveling machine
The leveling machine is compose of plate material guiding device,guide plate driving roller, adjustable guide device on both sides, leveling roller and etc.
The leveling machine have a separate motor drive and the speed is slower than main drive motor. In the head of the reducer shaft installed overrunning clutch.Firstly the  motor drive feeding material,then workpieces into main drive roller, and due to the effect of the overrunning clutch, the front drive motor is in a passive state.
Due to the main diver motor's speed is faster than front drive motor,when plate material cutting down,between the workpieces will have a distance.
When a batch of workpieces are finish, the steel coil needs to be remove,and the front drive motor will be stop.When all the finish workpieces are completely out of the roll forming machine, the front drive motor will inverse motion and  exit the steel coil.
3.Hydraulic punching device:Â
structure type:Hydraulic punching device rack is use gantry type. The power source is the pressure of under oil cylinder:The hole position is longitudinally fixed and can be adjusted transversely.
 Main parameter:
- Maximum punching plate thickness:3mm
- The horizontal adjustment range of punching hole distance :45~500mm
Function:After input the length parameter of workpiece through PLC,the encoder will counting length and when the workpiece length is enough the hydraulic cutting machine will cut down the workpiece.
Main parameter:
- Maximum cutting plate thickness:3mm
- Effective cutting width of workpiece:650mm
The roll forming machine is compose of drive motor, frame, forming roller,Manual regulating workpieces specifications device.
- forming roller driving motor using 15kw hardened gears reducer ,frequency control and encoder control brake.
- The frame uses the channel steel as the main beam,and the middle is welded by the stiffener plate.
- The forming roller is use the method of two sides formed and the form of middle cut off. The forming roller through the motor driven sliding screw rod to adjust the workpieces specifications. Between the two sliding screw rod use the bevel gear to drive and made them to achieve complete synchronization also with self-locking function. The thickness of the steel plate is adjusted by adjusting the eccentricity distance of the passive roller.
(3)Equipment production process
(1)The main technical parameter
1.Rolling product specification:width 100~300mm,high 40~80mm,thickness2.0~3.0mm
2.The speed of rolling:12-15 m/min
3.Number of sets of molding:17 sets main roller
4.Number of sets of leveling: 7 sets leveling roller
5.Transform line:2 sets
6.Installation form:Adopt arch type
7.Roller type: use split type
8.Roll material: GCr15 quenching treatment, HRC58-62
9.Spindle material: 45 quality steel quenched and tempered
10.main motor power:15KW
11.Hydraulic station motor power:7.5KW
12.Change the specifications speed: a full set of 10 minutes
13.The method of Cutting and punching:After forming then punching and finally cutting
14.The material of cutting knife and punching mold:Cr12 quenching treatment.
15.Electronic control system:The whole machine use  industrial computer PLC Siemens frequency conversion to control.
16.Main machine size:length 11m×width 2.3m×high 1.6m (including main motor)
17.Total weight of equipment:Around 12000kg
(2)Composition of equipment:
1.Guide
To prevent the plate move in production process to keep the product quality.
- leveling machine
The leveling machine have a separate motor drive and the speed is slower than main drive motor. In the head of the reducer shaft installed overrunning clutch.Firstly the  motor drive feeding material,then workpieces into main drive roller, and due to the effect of the overrunning clutch, the front drive motor is in a passive state.
Due to the main diver motor's speed is faster than front drive motor,when plate material cutting down,between the workpieces will have a distance.
When a batch of workpieces are finish, the steel coil needs to be remove,and the front drive motor will be stop.When all the finish workpieces are completely out of the roll forming machine, the front drive motor will inverse motion and  exit the steel coil.
3,Hydraulic punching device:Â
structure type:Hydraulic punching device rack is use gantry type. The power source is the pressure of under oil cylinder:The hole position is longitudinally fixed and can be adjusted transversely.
Main parameter:
- Maximum punching plate thickness:3mm
- The horizontal adjustment range of punching hole distance :45~500mm
- Hydraulic cutting device:Â
Main parameter:
- Maximum cutting plate thickness:3mm
- Effective cutting width of workpiece:650mm
- Roll forming machine capable of quickly changing type:
- forming roller driving motor using 15kw hardened gears reducer ,frequency control and encoder control brake.
- The frame uses the channel steel as the main beam,and the middle is welded by the stiffener plate.
- The forming roller is use the method of two sides formed and the form of middle cut off. The forming roller through the motor driven sliding screw rod to adjust the workpieces specifications. Between the two sliding screw rod use the bevel gear to drive and made them to achieve complete synchronization also with self-locking function. The thickness of the steel plate is adjusted by adjusting the eccentricity distance of the passive roller.
(3)Equipment production process
feeding  -  guiding  -  leveling -   punching -   cutting  - forming -  tropsch feed
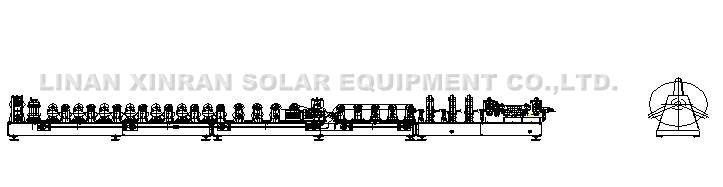
FAQ
1)Q:Can you make machine according to my design?
  A:Yes, we have experienced technical team to work out the suitable design for you and confirm with you until you agree.
2) Q: Will you deliver the right goods as ordered? How can I trust you?
  A: Yes, we will. The core of our company culture is honesty and credit.
3)Q:What payment terms you accept?
  A:Commonly is TT, 30% deposit and 70% before shipment, and sometimes we can consider more for you as per your request.
4) Q:What is the warranty for our machine?
  A:We have one year guarantee, and provide whole life's technical support.
Product Name:Prestressed hollow square pile mould
Size/Material:steel
Products Description:Prestressed Hollw Square pile mould which is used to produce the hollow square pile, this kind of Hollow square pile in the process of production, it use tension prestressed, reperfusion concrete and then use Centrifugal Machine to spinning the water out, because of this processing that makes reinforced prestressed hollow square pile is higher than other type of pile, at the same time, the pile body used the high strength concrete (C60, C80), high strength steel and high strength concrete in the application of hollow square pile production, make the performance of the pile, the bearing capacity and crack resistance, bending resistance are obtained significantly higher.
Application:Produce prestressed hollow square pile
Technical parameters:F250-F800
Concrete Hollow Square Pile Mould
Steel Piles,Reliable Square Pile Mould,Thailand Square Pile Mould,Concrete Hollow Square Pile Mould
Jiangsu Haiheng Building-Materials Machinery Co.,Ltd , https://www.jshaiheng.com