Â
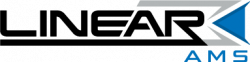
- Customer: Linear Mold & Engineering
- Industry: Mold Making
- Solution: Moldex3DÂ eDesign
- Country: USA
Why Choose Moldex3D?
Conformal cooling is a process in which we utilize 3-D printing technology to make cooling lines incorporated into a component of a tool. The reason for this process is applied to any portion of the tool that has a tendency of not cooling at a rate with the rest of the tool, in which problems like warpage occur. The result is having created cooling lines where never before possible, giving us even cooling throughout the entire tool.
In the molding analysis arena, we use Moldex3D as our software of choice. As a designer at Linear, I have been using Moldex3D since its introduction into our company in 2012 to analyze different methods of cooling and various press requirements that will be needed while still in the design process. After attending the classes that Moldex3D offers, I have become efficient in evaluating our approach to the design of the tooling we build. Using Moldex3D I can supply the information that will result in an appropriate build of a tool from the beginning to end.
One of the advantages I have found using Moldex3D is comparing conventional cooling to conformal cooling. By using Moldex3D, we can identify hot or cold spots in a tool before design has even been completed. The conformal cooling process is achieved through our 3-D printed metal process. A wide range of components can be created using this process from slides to inserts and virtually anything we can imagine. As they are created, cooling lines are built into the inserts allowing cooling that has never before been possible. As this process allows cooling exactly where we want it, the run time of tools can be reduced by over 50% in which a higher production volume can be achieved. In a recent comparison we were able to reduce cycle time of a tool from 35 to 16 seconds, resulting in a 54% reduction. A savings of 19 seconds per cycle over 350,000 parts led to a total savings of 1,847 hours (76 days of production). Creating these components with 3-D printing can also produce threading, thus reducing assembly time and cost.
       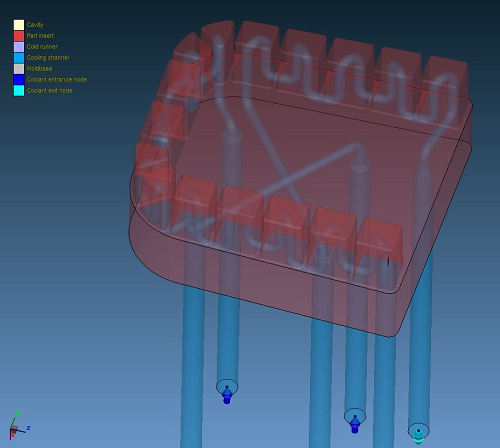
Conventional cooling vs conformal cooling
We have also found that dealing with warpage of the part can be controlled with the results from running Moldex3D. The results are tools that have been built to nearly perfect specifications with accounting for warpage and cooling of the tool before it has left the design room floor.
From my perspective at Linear, the Moldex3D software stands alone in the molding analysis world. The first thing that I noticed was how easy it was to use this software. Because of the user friendly graphics interface, I found the menus to be very simple to navigate. Also, the Moldex3D icons make finding a given function obvious. With no prior experience in this software, I was able to easily begin creating my first analysis with no formal training. After completing a few short classes provided by Moldex3D, I was able to successfully navigate through the entire software without confusion.
After using the software for some time, another great feature I discovered was the fact that I could customize my parameters for any of the analyses I wished to perform. As a more experienced user, I found it possible to predict conclusions that matched the physical outcomes with almost identical results. Another plus was the simplicity of the results and how easy they were to read. The answers to my questions were there in plain sight. I firmly believe that any designer with little to no experience could understand and interpret this software with very little effort.
If I haven’t convinced you yet, I found an abundance of uses and applications of Moldex3D including filling, packing and stress of the desired part. These features provide the benefit of predetermining information used in the molding process. Some other examples of how the software helped us at Linear include determining the press size and the amount of clamping tonnage that is required to run a particular tool, as well as predicting run time and pressure required for filling the part. With information that Moldex3D provides, you too can get perfect parts on the first or second shot.
Aluminium Industrial Profiles,Radiator Alu Profile,Bike Rack Alu Profile,Alu Profile Aluminium Rack
Jiangsu Yuejia Metallic Technology Co.,Ltd , https://www.yuejiametal.com