Residual or internal stresses are inherently induced within plastic products during manufacturing processes; especially, polymer chains are highly oriented under the high deformation rate during the injection molding process. Â Most of the time, residual stresses could compromise end-use performance of products, such as impact strength reduction, poor chemical resistance, reduced wear resistance, environmental stress cracking, etc., causing undesirable properties such as dimensional distortion or optical birefringence (shown in Fig. 1). Â An industrial practical solution for this kind of manufacturing problem is called annealing. Â Annealing is the process that can relieve internal stresses of plastics by slowly heating and cooling plastics below its glass transition temperature or softening point.
Fig. 1Â Simulated retardation effect of flow induced chain-orientation and photo-elasticity.
In general, annealing process includes the following stages: (1) placing the plastic part in an annealing oven; (2) heating the part to the annealing temperature at a controlled rate (commonly less than 1 ºC/min); (3) holding the part at the annealing temperature for a specific period of time, depending on the types of polymers and the thickness of products; usually from few hours to few days; (4) cooling the part to the room temperature at a rate lower than 0.5 ºC/min. There are usually two kinds of annealing process for plastics: batch annealing and continuous annealing processes.  The batch process is the most common one, which plastic parts are placed on the shelves/racks in a temperature controlled oven. Moldex3D Stress provides annealing simulation tool to help users understand the process (see Fig. 2).
Fig. 2 Â Moldex3D annealing simulation.
Based on the need of product quality management, Moldex3D Stress provides  warpage and stress analysis under the influence of annealing. Furthermore, evaluating dimensional variation of parts during annealing process can also be achieved through Moldex3D as shown in Fig. 3 and Fig. 4. In addition to the Moldex3D Stress Annealing simulation solution, Moldex3D Material Lab provides a full spectrum of material characterization of viscoelastic properties for stress analysis. Users can choose linear elasticity theory for quick analysis or viscoelastic theory for more accurate analysis.
Fig. 3 Â Simulated residual stress before and after annealing process.
Fig. 4Â Â Control geometry precision through annealing stress analysis and warpage analysis.
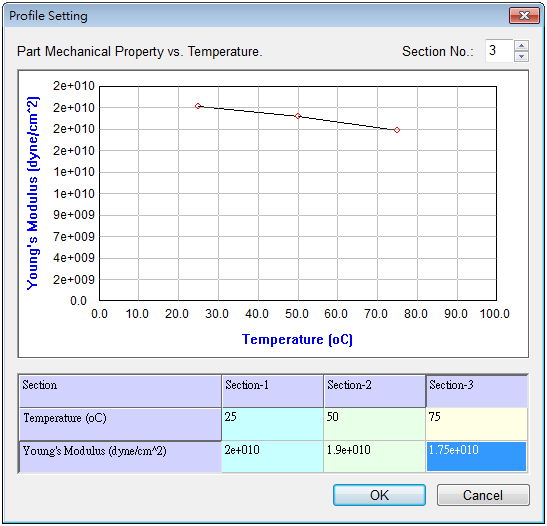
Fig. 5 Â Linear elasticity theory and viscoelastic theory in stress analysis is available in options for annealing process.
Blind Flange,Blind Flange Pipe,Spec Blind Flange,Blind Flange Adapter
Jiangsu Solid Machinery Manufacturing Co., Ltd. , https://www.oilsolid.com