The process of a dyno test on a Liebherr engine
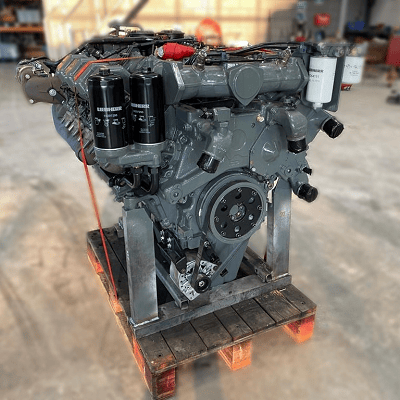
When it comes to heavy machinery, reliability and power are paramount. Liebherr, a name synonymous with innovation and excellence in engineering, stands tall as a pioneer in the realm of heavy equipment and machinery. From towering cranes to robust excavators, Liebherr’s engineering prowess extends to the heart of these machines. We delve into the world of dyno testing a Liebherr engine, uncovering the meticulous process behind unleashing the raw power concealed within.
The foundation of excellence
Before we embark on the journey of dyno testing, it’s crucial to understand the foundation upon which Liebherr engines are built. With decades of engineering expertise and commitment to quality, Liebherr engines are crafted to withstand the most demanding environment and deliver unparalleled performance. Each component is meticulously designed and rigorously tested to ensure reliability, efficiency and longevity.
The process
1 Preparation: The engine undergoes meticulous preparation before being mounted onto the dynamo meter. This includes ensuring all connections are secure, fluids are filled to the appropriate levels, and sensors are properly calibrated.
2 Mounting: The engine is carefully mounted onto the dynamometer, a specialized device designed to simulate real-world operating conditions. Precision is paramount during this step to ensure accurate results.
3 Initial checks: Once mounted, a series of initial checks are conducted to verify proper alignment, connection integrity, and functionality of all engine systems.
4 Warm-up: The engine is started and allowed to warm up to operating temperature. This ensures consistent results and minimizes the risk of damage during testing.
5 Baseline testing: With the engine warmed up , baseline tests are conducted to establish initial performance metrics. This includes measuring power output, torque, fuel consumption, and emissions at various RPM levels.
6 Load testing: The engine is subjected to progressively increasing loads to simulate different operating conditions, such as idle, partial load and full load. This allows engineers to assess performance across the entire operating range and identify any potential issues or optimization.
7 Data analysis: Throughout the testing process, data is continuously collected and analyzed in real-time. Advanced instrumentation and software are used to monitor performance metrics and identify trends or anomalies.
8 Optimazation: Based on the data analysis, adjustments may be made to optimize engine performance. This could involve fine-tuning fuel injection timing, adjusting air-fuel ratios, or optimize turbocharger boost pressure.
9 Validation: Once testing is complete, the results are meticulously reviewed and validated against predetermined criteria and specifications. Any deviations or anomalies are thoroughly investigated to ensure accuracy and reliability.
10 Reporting: Finally, a comprehensive report is generated detailing the results of the dyno testing, including performance metrics, observations, and any recommendations for further optimization or refinement.
The outcome of dyno testing
Dyno testing a Liebherr engine is more than just a routine procedure – it’s a testament to the unwavering commitment to excellence that defines Liebherr’s engineering philosophy. By subjecting their engines to rigorous testing and analysis, Liebherr ensures that each engine delivers the uncompromising performance, reliability, and efficiency that customers expect.
In conclusion, dyno testing a Liebherr engine is not just about measuring power output. It’s about unlocking the true potential of these remarkable engines and ensuring they exceed expectations in the most challenging environments imaginable.
â—† Handle design, easy to carry and emptying.
â—† Self-closing lid design to keep it closed when not in use so as t o isolate wastes from fire source and limit the amount of oxygen ,therefore to eliminated
effectively the risks of spontaneous combustion.
â—† High-quality galvanized steel structure (0.8mm thick)with epoxy resin coating on both inside and outside walls to make the product more durable and
chemical resistant.
â—† The cylindrical structure and heightening type bottom can promote the flow of air around the bucket.
â—† Pedal design to liberate hands in operation.
â—† Different sizes of oil waste can meet the use of different environmental requirements. It is very convenient to make choice.
Biochemical Trash Can
Biochemical Trash Can is suitable for most hazardous chemicals such as solid waste, solvents, waste wipes, debris and other materials in a short-term manner, in order to prevent spontaneous combustion, and can be used independently or with a chemical-resistant treatment bag.
â—† Polyethylene HDPE molding, durable and corrosion resistant. There are two choices of red and yellow colors, with labeling of
biochemical hazard.
â—† The bucket can store rags or wipes impregnated with solvents, substitutes, linseed oil, flammable adhesives and other flammable
liquids.
â—† Cover opening of foot control, which is able to close automatically. When it is closed, the contents inside are isolated from the fire
source, limited amount of oxygen would prevent the combustion from continuing, and eliminating hidden dangers.
Huanawell ZOYET Industrial Products cover a ideal range of applicable lines that could be used in Flammable, Corrosive Secure Storage, Hazardous Material Keeping, Circulation, Spill Prevention, Control & Counter Measure (SPCC), On-spot Working Safety and Efficiency Improvement, Personal Safety Protection etc. processes and occasions.
The products conform to UL, EN, OSHA, NFPA, EPC, NPDES standards relevant to various industries.
Huanawell is an emerging name and leading global provider of products, services, and solutions for lifeplace, – whether it is an office, home, school, factory, or public facility, even a car.
Wuxi Huanawell Import & Export Co., Ltd. is such an entity, establishing and figuring out resources and catalysts to help customers work better, live better with peace of mind. We are striving creating values needed by the clients in both industrial & civil sectors, which help them be more productive, including with the latest technology, core office supplies, facilities products, furniture, and all possible security solutions. The company also provides a variety of services including sourcing & outsourcing in relevant industrial and civil areas.
The company serves consumers and businesses in over 23 countries with more than 35 local distributors or dealers, and a dedicated business-to-business sales organization – all delivered through a regionally connected network operations, joint ventures, franchisees, licensees and alliance partners. The company operates under several banner brands including ZOYET, Huanawell, Golden Knight etc. Huanawell Imp.& Exp. features products from safety storage cabinet, safes, fireproof boxes, safety cans & containers, SPCCs (spill prevention, control & countermeasure), PPEs(personal Protection Equipments), Monitor Cameras...
The Huanawell`s overall focus is to meet the rising demand for increased security with a product-driven offering centered on the customer.
We achieve this through our primary product areas, the traditional segments of industrial storage, maintenance, repair,operation -MRO, and security solutions with safes, fire filing cabinets, access control etc.
Huanawell's strong growth comes from: long-term structural development in mature markets in China, South America, Africa and Asia Pacific; increasing demand in emerging markets in Asia, eastern Europe, Africa and South America drives us in this way aggressively; and successes in fast-growing product segments.
The strategic action plans have been divided into three focus areas: market presence, product innovation and cost-efficiency.
We call our business strategy `the INTEGRATION`, since it sets out a constant path for us for the long term. First developed in 2012, it was formalized in 2013 but its core elements remained the same. The strategy lays out our ambitious purpose and vision:
Purpose: to strive for a better lifeplace"
Vision: to be one leading brand and supplier for industrial and civil security products, whilst reducing our environmental footprint and increasing our positive social impact"
The INTEGRATION also defines four non-negotiable commitments within the business that we believe will help us achieve our purpose and mission: to provide industries and consumers necessary products and solutions to secure a better lifeplace with peach of mind.
Products which are sustainably made, sourced and used in a way which protects the earth`s natural resources
Respect for the rights of the people and communities we work with throughout the world. To protect both people's property and life, in daily and work environment.
Industries and Market
The industries and Market we served include but not limited to below areas.
Construction, Logistics& Warehousing, manufacturing, Chemical, Petroleum, Electrical & Electronic, Metallurgy, Food, Medical, Pharceutical, Labs., Agricultural, Power Generation, Financial Service, Commercial, Government divisions, Public & Private sectors
We work to create a better future every day, with brands and services that help people live good and work safely, and get more out of life.
Ready to respond to your request correctly and in time
Quick response, ensured quality, as short leadtime as possible, smooth delivery is what we are striving for.
Such services are supported by our serial resources and expertise in the industries and solutions, consisting of Manufacturing, OEM/ODM, Design & Development, Agency Service, Sourcing & Outsourcing, Procurement etc., which are across in construction, chemical, petroleum, electrical & electronic, medical, pharceutical, agricultural, power generation, real estate, government division, civil & private sectors.
Manufacturing
Manufacturing is one of our key elements in the business. Most of out manufacturing facilities and process are equipped with modern advanced machinery, techniques & technology, with ISO approved Quality Management System latest approved.
Based our regular lines of products, private label products and designs are possible to be considered for authorized production, based on mutual negotiation.
OEM/ODM
OEM - original equipment manufacturer, denote us the position for manufacturing the client's specific need of product, as long as such product could fall into regular lines of manufacturing process & resources. And OEM cooperation is based on mutual negotiation with Confidential/Non-disclosure Agreement.
ODM - original design manufacturer, allow us the mission to customize solution client outlined. It has more complicated service chart apart from similar process as that OEM required, thus requiring better mutual understanding and cooperation.
Agency Service
We also represent some of famous brands or manufacturers in the industries, for the marketing and sales activities in the global market. Such agency services enable us not only to represent us but to penetrate the markets where our principals do not have edge to attain to separately.
Sourcing & Outsourcing
Sourcing & Outsourcing are the two sides of one hand. Sourcing help us a lot in the regular business that help meet the solution requirement, fixing our extra or supplementary demand of materials, products etc. Meanwhile, outsourcing would definitely maintain our clients' various needs satisfied, which extend our vision in the industries.
Chemicals Waste Cans,Safety Cans,Chemical Waste Containers,Laboratory Chemical Waste Management Procedures
Wuxi Huanawell Metal Manufacturing Co., Ltd. , https://www.wxhnwmetal.com