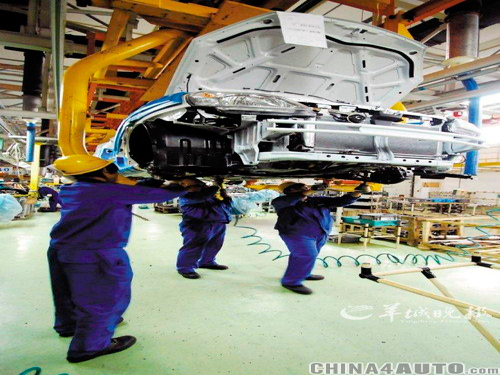
Commercial vehicles have been “victimized†for the most part. In the past year or so, steel prices have remained high at high prices, rising as much as 40%-50%. Whether it is from the domestic or from the international raw material market, Chinese auto companies must face the cost pressure brought about by the long-term high raw material prices.
It is understood that the amount of steel used for bicycles in automobile manufacturing is about 0.8-1 tons, which accounts for 70% of the cost of raw materials; the amount of steel used for medium-sized trucks is about 3.6 tons, which is obviously affected by steel prices; and heavy commercial vehicles are subject to steel prices. The impact will be even greater.
In this regard, a person in charge of Shaanxi Heavy Truck Co., Ltd. said in an interview with the media that for heavy trucks, it is very sensitive to the rise in steel prices. At the end of last year, the cost per vehicle increased by several thousand yuan. Companies will absorb their own costs by reducing costs, increasing efficiency, and then improving management. Yutong bus representatives also said: "The rise in steel prices will certainly have an impact on costs, will relatively take up profit margins, but the company will work through its own efforts to absorb cost pressures and temporarily do not plan to adjust vehicle prices."
The shrinking profits of cars Compared to commercial vehicle companies, the days of car companies are much better. It is understood that due to the different market conditions and the continuous rise in the price of steel products, different car manufacturers have different levels of influence. Among them, the profits of luxury cars and mid- to high-end cars are relatively abundant, and the proportion of steel costs is relatively small. At the same time, such companies shift the cost pressure of components as far upstream as possible, and thus the impact is relatively small.
However, under the double pressure of sharp price increases of raw materials and drastic price cuts by cars, the profitability of the Chinese auto industry, which has always been known as “profiteeringâ€, has also been narrowed. Having used a lot of money to make money, Chinese car companies that have spent so much money on their "broad-bones" life have also begun to learn the days of careful planning.
In an interview with the reporter, Zhou Zhihua, chief representative of KIA South China, said that Dongfeng Yueda KIA has actively raised the localization rate of steel used to reduce production costs to ease the impact of the shortage of the international steel market on production.
A related person from the Department of Public Relations of Changan Ford said in an interview with reporters that since Changan Ford signed a long-term purchase and sales agreement in cooperation with steel manufacturers, it can purchase steel products at a relatively stable price, so it is currently impossible to guarantee normal production. problem. The person in charge of the market department of the Japanese automaker told reporters that more than 70% of the steel they currently use is mainly dependent on domestic steel companies such as Baosteel, Wuhan Iron and Anshan Iron and Steel, etc. Since they have established long-term contacts with these three companies, they can now guarantee steel production. Smooth supply of raw materials.
The low-end car was squeezed. However, smaller car makers are less fortunate. Due to the limited production and sales volume and incomplete supply chain, the shortage of steel raw materials may directly affect the production of the company. Moreover, due to the high cost of steel and the difficulty of upstream transfer of parts and components costs, low-end car manufacturers are relatively affected. For example, Jiangnan Alto sells for only 18,800 yuan, Geely Panda sells for only 39,800 yuan, and the profit margins for Hafei and Chery cars are relatively small, and raw material price increases will have a greater impact on their profits.
However, for the moment, there has been no increase in the price of auto raw materials, which has caused prices to escalate to consumers. On the contrary, many car manufacturers raised their price cuts, drastically reduced the price of economical cars, and made the competition more fierce.
Zhang Yong, an automotive marketing expert, analyzed that the rise in steel prices will further exacerbate the survival of the fittest in the automotive industry and accelerate the integration of resources in the automotive industry.
The difference between ASME/ANSI and API is the fabrication material and a higher rated API operating pressure.
ASME/ANSI flanges are commonly used in industrial process systems handling water, steam, air and gas. API flanges are manufactured for high strength operating refinery systems with products such as oil and explosive gases.
The flange standards API 6A and ASME/ANSI B16.5 have the same dimensions – but the API 6A flanges are rated for higher pressures as indicated below:
API vs. ASME/ANSI Flanges with ratings
|
Pressure Class Rating (psi)
|
|
||
---|---|---|---|---|
ASME/ANSI B16.5 | API 6A |
|
|
|
|
600 | 2000 |
|
|
900 | 3000 | |||
1500 | 5000 | |||
|
600 | 2000 |
|
|
900 | 3000 |
|
||
1500 | 5000 |
|
Api Flange,Api 6A Flange Factory,Api 6A Normalized Flange,Api 6A Std Flange
New Century Machinery Co., Ltd , https://www.ncmflange.com