What kind of modern thermal power plant is? When you enter a thermal power plant, people do not see people coming and going, and the unit's power generation and modernization management is quietly proceeding. At the scheduling meeting, the deputy general manager in charge of production was checking the operation status of the unit and the grid load before the large-screen projection with the production managers, and developed a new bidding price and equipment maintenance plan; the financial department was printing financial statements and forecasting new power generation. Cost; The Material Supply Department is reviewing material consumption and equipment loss, making spare parts purchase plans based on inventory, and publishing procurement information on the Internet; the inspection team is filling out work tickets online to apply for equipment maintenance; general manager on business trips; The company is using laptops to view the company’s data on the Internet and make the right decisions based on the conclusions of the analysis system. This is the scenario of a modern thermal power generation company. It is in stark contrast to the past heat, but it has produced several times the economic benefits. Although the number of employees is small and the benefits are high, every part of the company can produce the greatest efficiency. This is the dream of any thermal power plant business leader, and this can be achieved through the implementation of the integrated DCS (Distributed Control System) control project.
What is the integrated control and control of DCS? First of all, the overall technical route of the integrated system of management and control is: The system adopts WINDOWS NT and QNX operating system platform, adopts field bus technology, and forms the DCS system to carry out the whole process of production of thermal power units to every link. Monitor and control. On this basis, the functions of the thermal power plant enterprise resource planning (ERP) are integrated into the DCS through a real-time information system interface to form a computer system that integrates management and control. The system should fully adopt the field bus technology and open computer and network technology from the architecture. System structure diagram shown in Figure 1.
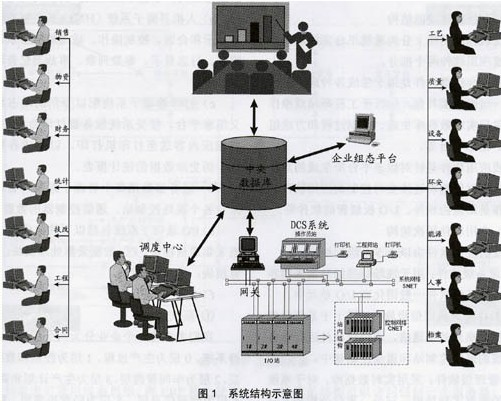
In thermal power companies, what are the objectives of using the integrated management and control system? First, using the philosophy of computer integrated manufacturing, the various resources of thermal power companies, such as people, finances, materials, and time, can be fully utilized to make power generation processes and enterprises The operation has been optimized to enable the company to gain an advantage in the market competition of “separate plant and network, and compete for pricesâ€. Through the implementation of the integrated DCS management and control project, the company's resources are integrated to achieve effective operation and management of the company. The advantages of the company's core competitiveness are fully utilized to reduce the cost of power generation and meet the needs of the power grid. The company achieves long-term economic benefits with safe and economical power quality and efficient, high-quality maintenance service. The benefits of implementing the integrated control and control DCS project are mainly reflected in: (1) reducing the cost of power generation production; (2) reducing management costs; (3) improving corporate profits; (4) improving the overall economic benefits of enterprises; Power, customer satisfaction rate.
Thermal power companies must achieve the above objectives, and what functions should the integrated management and control system have? Under the unified control and control integration of DCS engineering ideas, integrated automation technology, computer technology, network technology, information technology, intelligent technology and related processes (including power generation and maintenance And other processes) technology, the establishment of thermal power companies integrated business decision-making system, management information systems, production planning and scheduling systems, workshop management, on-site control and data acquisition systems. With the support of computer network and database management, not only integrate all production activities of power generation companies, including market analysis (such as: grid load analysis, power generation cost analysis, etc.), operation management, and production (including main business and tertiary production). It also integrates man-machine and establishes an integrated production automation system for business decision-making, production scheduling, workshop management, and production process optimization control. Therefore, the system should have the following main functions: (1) conventional detection function; (2) automatic control function; (3) advanced detection function; (4) integrated ERP function. In this way, we can achieve satisfactory business decision-making, information management, optimize production scheduling, optimize the operation and control of power generation processes, achieve energy conservation, reduce consumption, reduce costs, meet the requirements of power grids with safe and economical power quality, and improve the capabilities of thermal power companies in an all-round way. . This is why the integrated control and control program is implemented in thermal power plants.
Second, the management and integration system architecture and function
How does the management and control integration system architecture be implemented? We found that thermal power companies have two types of information, namely management data and field data. Management data can be distributed database management, on-site data is managed by DCS. The field data required for the management and the management data required for on-site control can be acquired and transmitted to each other. To this end, the system should be divided into three layers: control network, system network, and management network. The control network should use the most popular fieldbus network technologies (such as Profibus-DP and CAN, etc.), which are used to connect the field controller main controllers and I/O units; the system network is used to connect field control stations and operator stations. And the system server is used to complete the communication and data exchange between the site control station and the operator station and the server; the management network is used for data exchange between the DCS and the ERP and external data exchange.
1. System hardware architecture
The system hardware system should consist of DCS system hardware, ERP system hardware, and gateways. The DCS system hardware includes I/O stations, operator stations, engineer stations, servers, power cabinets, grounding cabinets, integrators, and the like. The ERP system hardware includes 2 to 3 servers, 100Mbps switches, integrators, and computer terminals.
2. System Software Architecture
(1) Architecture
Both DCS and ERP layer system software adopt the standard Client/Server structure. In order to maintain the consistency of the operation data (especially historical data) and maintain the security and large-capacity requirements of the system data, the operation layer of the system adopts the Client/Server structure. .
(2) System software function structure
The system software is divided into two parts: the system platform support software and the system online application software. The system platform support software is a set of configuration tool kits used to generate various application engineering environments, running on engineer stations or operator stations. Including real-time database generation, control process and method configuration, ERP configuration platform. Online application software is an application software for on-line real-time monitoring and continuous real-time control of objects generated by a configuration platform, including operator station monitoring software, I/O board-level intelligent software, and the like.
(3) Application Software Hierarchy
The system's application software consists of the following five levels:
a) Equipment-level software: Data acquisition and preprocessing for on-site signals, with equipment-level software generally solidified in I/O units.
b) I/O processing and communication level software: It is used for centralized data collection and external communication at the subsystem level. The communication level software runs in the field control station and communication controller of each subsystem.
c) Management level software: A real-time database is used to perform processing, recording, event analysis and other advanced application functions on subsystem or global data. The management level software runs on the system server.
d) Operation level software: The operation level is used for the system to monitor the thermal power field and realize the function of adjusting the process variable, parameter setting and soft hand operation. It is operated at all levels of operator stations, engineering stations and control stations.
e) ERP-level software: The ERP level automates the thermal power enterprise resource planning and runs on ERP servers and workstations.
System software should consist of six subsystems: system configuration, human-machine interface (HMI), print management, data central management, I/O communication, and ERP. In addition, GIS subsystems, video surveillance systems, voice query subsystems, voice alarm subsystems, and large-screen projection subsystems can be integrated.
a) The system configuration subsystem targets engineering applications and secondary development, providing two-level configuration functions.
1 Engineering application configuration: The engineering application is configured as a software package running on an engineering station or an operator station. It is a configuration tool for the user application environment.
2 Application Development Configuration: Provides a series of application development-oriented configuration tools to facilitate the addition or expansion of new application features.
b) The main functions of the human-machine interface subsystem (HMI) are graphical display and conversation, control operations, group trend display, process alarm, log display, parameter list, accident recall query display and printing.
c) The print management subsystem is equipped with a dedicated dynamic data definition configuration platform, accepts system server print commands and data, and sends the corresponding contents to the printer for printing to complete statistical reports of various real-time library and historical library data.
d) The server data management subsystem manages data from various field control stations and communication controllers.
e) The I/O communication subsystem includes the following software modules: 1 data acquisition communication module; 2 data acquisition and processing module; 3 calculation module; 4 communication module.
f) ERP management subsystem
1 Hierarchy
We consider dividing an enterprise into six levels and two supporting systems. Layer 0 is the production process, layer 1 is the control and data collection layer, layer 2 is the workshop management layer, layer 3 is the production planning and scheduling layer, layer 4 is the management information layer, and layer 5 is the management decision layer. ERP covers 2 to 5 layers of functionality.
Operational decision-making is a top-level function, based on the internal and external information of thermal power companies to provide decision support for business strategy, medium and long-term goals, development plans and annual comprehensive plans.
Management information can be further subdivided into business management, production management and humanistic management. Its task is to integrate management of production and business information of thermal power plants, workshops, and departments, and to form logical strategies based on the instructions of business decisions.
The production planning and scheduling layer completes the functions of production planning decomposition, production scheduling and production statistics, and further forms detailed production plans, production strategies and process strategies.
Shop floor management is the direct executor of production planning and scheduling. Mainly complete the production plan, control energy consumption, production statistics and so on.
The control and data acquisition layer implements routine control of the production process and basic data collection concerning production.
The database system and network system are the basis of the entire system, providing an integrated environment for system information integration.
2 functional structure
We consider that we can adopt the configuration idea to divide the ERP into functional modules according to functions. Each functional module is equivalent to an I/O station of the DCS. Through the enterprise configuration platform, the company's processes can be flexibly constructed to meet the needs of thermal power companies' changes. We can use a simple structure diagram (Figure 2) to represent the ERP functional structure.
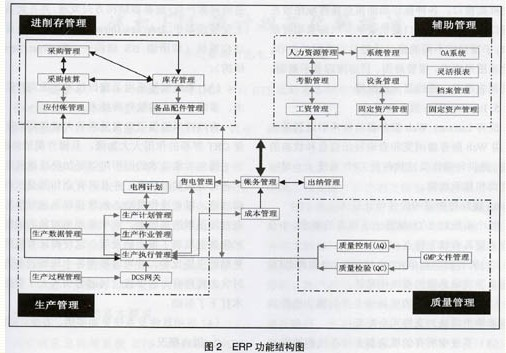
Third, key technologies to be solved in system implementation
Real-time data technology
The software platform adopted by the management and control integration system should organically combine the open Windows NT platform with the distributed embedded real-time multi-task operating system platform QNX to form a high-performance, high-availability real-time distributed control system. The on-site control station adopts the QNX system and is based on the process-oriented processing of the system. It has better real-time performance and reliability. The operator interface adopts Windows NT platform, which is based on the man-machine interface friendly operation and human factors performance. The Windows NT platform used by the server is based on the system's better scalability, data openness, and system integration with third-party software. The real-time database of the system should be based on the distributed server cluster technology. Through the transparent inter-process communication of the network, all the information of a geographically or functionally dispersed system can be formed into a global database. Any operator station can access any server. For local or remote monitoring and control.
Real-time network technology
In the integrated DCS system of management and control, the network is a key component of the entire system. The most critical of these is its reliability and real-time performance. The system's network is divided into three layers: site control network, system control network, and management network. The system control network is used to connect servers and I/O stations in the system. The field network is located in the I/O station and is used to connect the main controller module in the I/O station with each I/O module. The management network is used for data exchange between DCS and ERP as well as external data exchange.
3. Target-oriented graphics technology
In the software technology for the generation and display of power generation process simulation flow charts, object-oriented graphics design and programming techniques should be used, including the editing of graphical objects, the combination and decomposition of graphical objects, the dynamic characteristics of graphical objects, and the definition of human-computer interaction characteristics. And the management of graphics object library and other functions. Object-oriented graphical interface design technology can realize complex and beautiful graphical interface, and support animation function and graphic zoom function.
4. Multi-window technology
In software technology, a multi-window technology should be implemented. The background is a main frame window. Various operation screens are placed in the sub-window according to the operation sequence. The main frame window provides menus, status bars and background windows; the sub-window displays different contents according to different window functions, such as dynamic graphic pictures, alarm pictures, log tracking display pictures, parameter list pictures, curve display pictures, and the like.
5. Internet Web Server Technology
Internet Web server technology should be introduced into the system, with the Web server to browse and query on-site information and status functions, providing query and display functions corresponding to operator station software and ERP systems.
6. Hardware Design Techniques for Field Control Stations
The entire system puts high demands on the I/O station. The I/O station should have the following main features:
(1) All functional units (main controller, power supply and I/O) adopt a fieldbus-based modular design;
(2) The important modules in the system (main controller, power supply and analog output module) support redundant configuration;
(3) All modules in the system support online hot swap;
(4) The analog input module adopts 16-bit A/D converter, which has high common-mode and differential-mode noise suppression ability while maintaining high accuracy;
(5) The digital input module maintains a good noise suppression capability while achieving an SOE (event sequence) input signal resolution of 1 ms.
The above is the key technology in the implementation of integrated management and control systems for thermal power plants, and it is also the key to successful system development.
IV. Technical Development of Domestic and Foreign Systems
1. Foreign development
At present, the countries that can provide (integrate) the integrated management and control computer systems abroad are mainly Honeywell, Foxboro, and Siemens of Germany.
With the development of technologies such as computers, networks, and field buses, foreign DCS systems are constantly evolving and constantly improving. The characteristics of their technological development are as follows:
(1) The basic hardware and software have evolved from proprietary product systems to generic, standardized product systems.
(2) The system architecture evolved from a centralized structure to a distributed structure and then to a client/server structure, and on this basis, it developed into an enterprise-wide automation system based on Intenet/Intranet technology (the so-called BS structure—Browser/ Server structure).
(3) The system software adopts software technologies such as window technology, object-oriented technology, and multimedia technology.
The window technology provides a rich and flexible human-machine interface function, which greatly enhances the function of the CRT screen, and the operation is simple and fast.
The object-oriented technology graphics can more flexibly reproduce the real-time status of various parts of the factory, and has a three-dimensional map display and animation capabilities, so that operators can dynamically grasp the scene of the operation. On the basis of object graphics, object-oriented programming and object databases have been greatly developed in recent years. This makes computer software closer to field devices, and can provide powerful means according to the real-time status of various field devices, and at the same time introduce labor. Smart technology lays the foundation.
(4) The application software and system are more practical, convenient and reliable.
2. Domestic Profile
At present, apart from Beijing and Lees, there is no second company's product that can achieve seamless management and control, and integrate enterprise management and control. However, in thermal power companies, there is very little implementation of integrated control and control programs.
3. Technical comparison of domestic and foreign systems
The level of technology and systems used by domestic manufacturers is compared with the most advanced foreign technologies and systems of the same level. The level of system foundation, architecture, software technology and application design basis are similar, but in the business operations, decision-making modeling and There is still a gap in application.
V. Conclusion
According to the comparison of system technology and cost-performance ratios, thermal power companies can implement integrated management and control programs to give priority to domestic products. Because in the system foundation, architecture, software technology level and application design basis, domestic products have reached the international advanced level, and can achieve seamless connection, and ERP management subsystem can be easily modified and upgraded according to needs. However, in implementing the integrated management and control program for thermal power plants, regardless of the use of domestic manufacturers or foreign advanced products, attention should be paid to the following issues:
(1) When formulating a thermal power enterprise's integration of management and control plan, advanced modern management ideas should be embedded in the integrated system. This is the difficulty of the plan, and it is also the key to the success of the implementation of the system. It is the basis for raising the level of thermal power enterprises in an all-round way.
(2) Nowadays, more and more thermal power companies have incorporated the idea of ​​status overhaul into daily maintenance and maintenance of power generation equipment in order to adapt to the new development situation. Through the monitoring and diagnosis of equipment status, the pre-diagnosis of equipment faults is realized. And life expectancy, so as to reasonably arrange equipment maintenance plan, ensure equipment safety, economy, long-term operation. Current diagnostic techniques and means for the state of equipment have matured, but there are still no mature theories and mathematical models for the prediction of equipment failure and longevity. In addition, the analysis of the impact of the equipment on the cost of power generation under the conditions of failure and reduction of output power cannot still use quantitative analysis instead of qualitative analysis. Therefore, when implementing the integrated system of management and control, an accurate and reasonable state maintenance mathematical model should be established so that the system can be fully integrated into the daily work of thermal power companies to maximize their effectiveness.
(3) Due to its uniqueness, thermal power generation enterprises have long maintained stability in their management systems and institutions, and it is difficult to implement advanced management ideas. Many thermal power companies put the current management system into the system when implementing the MIS system project, which has restricted the effectiveness of the system. Therefore, in the process of implementing the integration of management and control, how to incorporate advanced management ideas into the management system of thermal power companies is a problem that must be solved in order to ensure the maximum utilization of system efficiency and to promote the overall improvement of thermal power enterprise capabilities.
(4) In the process of integration of management and control, the full integration of the system and the enterprise is an urgent problem to be solved. In thermal power companies, there is a big gap between the scope of work and the level of use of systems that are faced by the four majors (vehicle, boiler, electrical, and thermal) of operation and maintenance, especially maintenance. Therefore, it is imperative to implement targeted all-round training and adapt the employees to the system so as to ensure the maximum "expansion" of the system.
Zinc Die Casting Products are a metal forming process in which molten zinc metal is put under pressure and injected into a die.
Zinc are alloys that have high strength and hardness, outstanding corrosion resistance,full recyclability, mechanical properties, high thermal and electrical conductivity and strength at high temperatures. Zinc alloys possess high dimensional stability for complex shapes and excellent thin walls. The cost of raw material is low.
Zinc Die Casting Products are efficient and economical and offers a wide range of durable shapes and components. Little or no machining is required after a part is die casted, because the process provides very close tolerances for even complex shapes. Zinc Die Castings can also be easily plated or finished. Zinc Die Casting Products are dimensionally stable and heat resistant.
Although this alloy exhibits excellent casting characteristics, it has seen limited use by die casters. It does however possess some interesting characteristics that may be of assistance to designers. Its creep performance is rated higher than the other zinc alloys and it maintains higher strength and hardness levels after long-term aging.
The behavior of zinc alloys under stress is non-linear and time-temperature dependent on strain-rate, i.e. the ratio of stress to strain is not constant, even at low stresses, and varies with time resulting in continuous plastic flow under constant applied load. Designers of structural components should be aware of the creep limitations of zinc alloys, which do not have a single value for elastic modulus or yield strength. Yield strength (allowable stress) under sustained loading is dependent on the allowable design strain (% elongation) over the required service life. Working values for the elastic modulus and yield strength are important for design purposes. Standard engineering formulae used for calculating cross-sections of elastic materials must therefore be used with some caution.
This alloy exhibits excellent damping capacity and vibration attenuation in comparison with Aluminum Die Casting alloys.
We have professionally produced Zinc Die Casting Products nearly 7 years. The parts have a great property of high quality, high precision, reasonable competetive price. our products are very popular.
Zinc Die Casting Products
Zinc Die Casting, die casting parts, Zinc Alloy Die Casting, Zinc Casting, Hardware Parts, Valve Parts, Auto Parts
NINGBO ZHENHAI BOLANG METAL PRODUCT FACTORY , http://www.bldiecasting.com