The submersible sewage pump and the motor are coaxial, the shaft is short, and the weight of the rotating parts is light. Therefore, the load (radial) on the bearing is relatively small, and the service life is much longer than that of a general pump. There are no problems such as cavitation damage and water diversion. Small vibration and noise, low temperature rise of the motor and no pollution to the environment.
Since the motor of the submersible sewage pump is used for diving, the key point of the equipment is to prevent the motor from entering the water. Once the motor enters the water, the bearings, windings, and insulation are damaged, causing the motor to be burned, increasing maintenance costs and maintenance time, and affecting production. Therefore, it is very important to ensure that the motor seal and leakage protection device are normal.
The IP68 protection level is usually used. Although this level is very high, the reason for the inflow of the motor cannot be avoided. There may be many reasons for the water entering the motor. Commonly there are the following:
1, the cable is broken
2, submersible sewage pump mechanical seal damage
3, cable or motor sealing device leaks.
Once the motor system enters the water, bearing will appear, the unit will be short circuited, and even the entire motor will be burned.
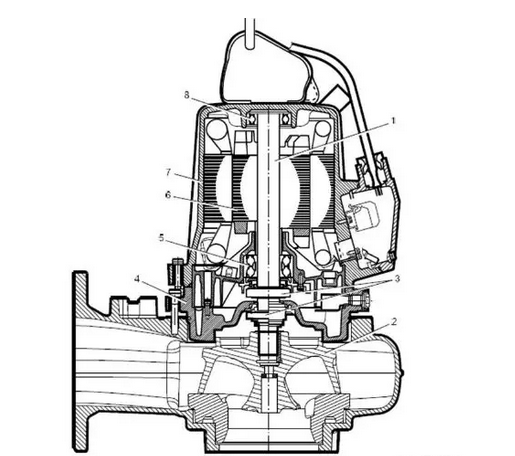
The case analysis site is located in Chongqing and is mainly used for pumping domestic sewage.
Fault phenomenon
In February 2018, the customer feedback that the two sewage pumps would not start, the No. 1 pump would trip on power-on, No. 2 would not start, and the site would need to be started urgently and rushed to the site to check and found the following problems:
(1) No. 1 submersible sewage pump three-phase resistance AC2.2 Europe BC2.6 Europe AB1.9 Europe, ground insulation 0.2 megohm, can not start the pump, the need for motor repair. No. 2 submersible sewage pump three-phase resistance AB2.8 Europe, AC2.4 Europe, BC2.7 Europe, can start.
(2) lift up the No. 2 pump and found that the pump inlet stuck a piece of wood, there is more water in the motor terminal box, there is a small amount of water in the motor coil, drying a few hours of insulation> 550 megohm, because the site can not stop the pump Install back and use it temporarily. After the No. 1 submersible sewage pump is repaired, it is required to dry the motor and replace the motor bearing. Pump No. 1 was lifted. A large amount of water was found in the motor terminal box. It was found that there was more water in the motor coil and the internal coil of the motor burned off.
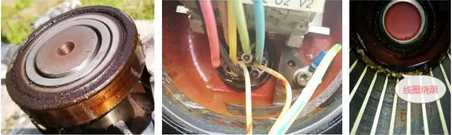
(3) Disconnect the cable junction box and the terminal has rusted. The incoming cable did not use the Glan head to get stuck in the cable sheath and the seal was seriously insufficient. The site needs to be replaced with two junction boxes for reliable connection, good sealing performance and adaptability to the wet environment.
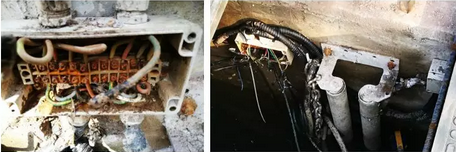
Fault phenomenon
The two submersible sewage pump motors were burned and the incoming water was not sealed in the transition junction box. The moisture in the sewage pit was very large. The relay junction box and the cable were subject to moisture condensation and accumulated in the relay box and cable. The cable inside penetrates into the motor terminal box and the motor coil short circuit burns the motor. In addition, there was no oil-water mixture in the motor to eliminate the leakage of the machine seal, and there was no leakage of water in the cable and the motor sealing device. Should be caused by improper site installation!
According to statistics from the manufacturers, the pump housekeeper reports that submersible pump motor water inflow failures are caused by cable damage or water ingression of more than 70%. It is important to prevent and strengthen monitoring.
Prevention and overhaul
Inspection of motor seals and protective devices:
The submersible sewage pump has a good protection device, there will be an alarm when there is a sealing failure, and maintenance personnel need to timely repair, of course, but also according to the inspection cycle to do the following checks:
(1) Check the insulation resistance of the pump motor windings to ground. Periodically check the insulation resistance between the motor windings of the water pump, and its value should be greater than the insulation value requirements of the instructions at different temperatures, otherwise it should be disassembled and overhauled. If the incoming water is to be dried, check that the ground is solid.
(2) The oil chamber seal condition. After the sewage pump is used in the specified medium for half a year, the condition of the oil chamber shall be sealed. If water (milk emulsion) is found in the oil, clean the oil chamber as required, and refill the oil to replace the oil of N10# or N15#. The oil can be added to the oil filling port to overflow. If necessary, replace the mechanical seals. For the sewage pump used under severe working conditions, it should be overhauled. If the leaking probe is alarming for a short time after oil change, the mechanical seal should be overhauled. If the mechanical seal is damaged, it should be replaced or overhauled.
Seal damage occurred, protect the device troubleshooting
The mechanical seal will inevitably have a certain amount of leakage. If the oil in the oil chamber is replaced in time after the leakage alarm, the alarm can be cancelled. If the lubricating oil is not replaced in time, not only the alarm will continue, but also the sewage will accelerate the mechanical seal on the motor side. The sewage will enter the motor, reduce the insulation of the motor and even burn the motor, causing huge losses. If the overheated component needs to be replaced due to burnout, the corresponding components may be replaced if the float switch is damaged. The leaking probe and the sealing device may be excluded as such.
(1) Check for failure of leaking probe. The failure of the leaking probe is usually caused by the blowout of the wire of the leaking probe. During inspection, the epoxy filler in the copper pipe of the leaking probe is dug out first, and then the lead-out line is turned on to make each lead wire conductive and insulated from each other. Finally, the epoxy resin was poured into the copper tube, so that the leak probe was re-created. After the lead wire on the probe is firmly connected with the bolt, it is led to the outer junction box together with the power cable of the motor to ensure effective monitoring of the leakage.
(2) Overhaul of seal leakage. Leakage failures of submersible pumps are mostly due to aging and wear of the sealing device. In addition to replacing new seals, the following simple elimination methods can also be used:
1 If the submersible pump seal loses its elasticity due to long-term use, remove the seal at this time, and then find a 0.3~0.5mm thick paper or cloth cut into the groove slightly larger than the original seal ring, and finally install Upper seal ring.
2 If the rubber seal in the nylon seal seat is worn, the seal can be removed and then replaced. If the fastening spring on the seal loses elasticity or breaks, remove the spring and use a suitable diameter wire or wire to tie it. tight.
3 If the seal ring is seriously worn, the nylon seal can be taken out, and the asbestos rope coated with butter is then wrapped around the stainless steel sleeve to fill it slightly higher than the original nylon seat. Then, the butter is filled and the nylon seat is pressed and compacted with bolts.
4 If the seal between the seal box and the cast iron loses its elasticity, remove the seal ring from the cast iron groove and find a piece of 0.6~lmm thick paperboard shell cut to the same size, and then place it in the groove, and then put the seal ring again. Into.
5. If the oil hole rubber seal is damaged, you can find a piece of tape, cut it into a hole slightly larger than the bolt, add a flat pad on the top, and put it together in the oil inlet hole.
Atv Wheel ,Four Wheeler Wheels,4 Wheeler Rims,Atv Rims
JIANGSU DONGZHIBAO AUTOMOBILE CO.,LTD , https://www.dzbwheels.com