mold temperature controller
Application
This Mold Temperature Controller has been designed to maintain a constant temperature, using water or oil as medium. Mold temperature controller is used to control temperature in various industrial fields, such as: Reaction kettles, extrusion forming equipment, rubber forming machinery, cast film production lines, cable extrusion production lines, the dies for precise plastic molding, the dies for the compression casting of magnesium/aluminum/zinc alloy, roller pressing applied in rubber/plastic and leather industries, crude oil heating of the oil sinks on tankships, paper making industry, bottle blowing, and so on.Â
Oil type mold temperature controller use oil as a heat transfer medium, with indirect method to achieve heat transfer with advantages of large temperaure controlling range and nice thermal stability. Standard type models can reach to 200ºC, while high-temp type control to 300ºC, and the most up to 350ºC.Â
Relative to the oil temperature control system, the use of water as the media has its advantages: High heat transfer efficiency, less pollution, easy access to water resources, but the temperature range is small, up to only 98 ºC.Â
Developed by Hadrdega ultra-boiling water mold temperature controller, the temperature range has reached 120 ºC ~ 180 ºC and temperature control accuracy of ± 0.1 ºC make the use of water type temperature machine with a broader space.Â
Features
1. Casting shunt, to ensure uniform water
2. Perfect security protection, fault display
3. Explosion-proof equipment for pipelines
4. Microcomputer control board PID ± 1 ºC
5. Automatic air-exhausting function after startup
6. Optional: Air blowing and return water function.Â
7. Pump power &Â heating power can be customized
8. CNC main frame thickness 2mm, plate thickness 1.5mm, baking finish
9. Isolated electric box for longer service live, free from high temperature pollution
10. With imported overpressure protection &Â pressure display to ensure safety of pipelines
11. Heating pipe and pump electrical appliances adopts original Schneider Electric, with air switch
12. With reverse phase /Â phase shortage /Â water shortage /Â overload /Â over temperature /Â overpressure alarm function and by-pass pressure relief circuit.Â
Technical Specifications
Model MTC- |
6kw |
9kw |
12kw |
18kw |
24kw |
36kw |
|
Heat transfer medium |
Oil |
||||||
Operational temperature range |
60ºC~200ºC |
||||||
Heating power |
Kw |
6 |
9 |
12 |
18 |
24 |
36 |
Pump power (50Hz) |
Kw |
0.37 |
0.75 |
1.5 |
1.5/2.2 |
2.2/3 |
3/4 |
Max. Pump flow (50Hz) |
L/min |
42 |
56 |
110 |
112/160 |
160/220 |
220/330 |
Max. Pump Head (50Hz) |
M |
28 |
38 |
60 |
48/58 |
58/65 |
65/72 |
Heating tank No. |
1 |
1 |
1 |
1 |
1 |
1 |
|
Main oil tank capacity |
L |
5.3 |
5.3 |
7 |
10.6 |
14 |
21 |
Cooling method |
Indirect cooling |
||||||
Temperature precisioin |
±0.5ºC |
||||||
Display precision |
±0.1ºC |
||||||
Mould coupling |
3/8" (2X2) |
3/8" (2X2) |
3/8" (4X2) |
1" (1X2) |
1" (1X2) |
1" (1X2) |
|
Inltet /Â Outlet |
3/4" 3/4" |
3/4" 3/4" |
1" 1" |
1" 1" |
1" 1" |
1" 1" |
|
Dimensions |
L (mm) |
590 |
590 |
690 |
590 |
690 |
690 |
W (mm) |
295 |
295 |
310 |
590 |
620 |
930 |
|
H (mm) |
685 |
685 |
750 |
685 |
750 |
750 |
|
Weight |
Kg |
42 |
48 |
52 |
96 |
104 |
156 |
Technical Specifications------clean water
Model MTC |
6KW |
9KW |
12KW |
18KW |
24KW |
36KW |
|
Medium |
Clean water |
||||||
Operational temperature range |
Max. 100ºC |
||||||
Heater power |
Kw |
6 |
9 |
12 |
18 |
24 |
36 |
Pump power (50Hz) |
Kw |
0.37 |
0.75 |
1.5 |
1.5/2.2 |
2.2/3 |
3/4 |
Max. Pump flow (50Hz) |
L/min |
42 |
56 |
110 |
112/160 |
160/220 |
220/330 |
Max. Pump Head (50Hz) |
M |
28 |
38 |
48 |
48/58 |
58/65 |
65/72 |
Heating tank No. |
1 |
1 |
1 |
1 |
1 |
1 |
|
Heating tank capacity |
L |
4 |
4 |
6 |
8 |
12 |
18 |
Cooling method |
Direct cooling |
||||||
Temperature precisioin |
±0.5ºC |
||||||
Display precision |
±0.1ºC |
||||||
Mould coupling |
3/8" (2X2) |
3/8" (2X2) |
3/8" (4X2) |
1" (1X2) |
1" (1X2) |
1" (1X2) |
|
Inltet /Â Outlet |
3/4" 3/4" |
3/4" 3/4" |
1" 1" |
1" 1" |
1" 1" |
1" 1" |
|
Dimensions |
L (mm) |
590 |
590 |
690 |
590 |
690 |
690 |
W (mm) |
295 |
295 |
310 |
590 |
620 |
930 |
|
H (mm) |
685 |
685 |
750 |
685 |
750 |
750 |
|
Weight |
Kg |
42 |
48 |
52 |
96 |
104 |
156 |
Connection Diagram
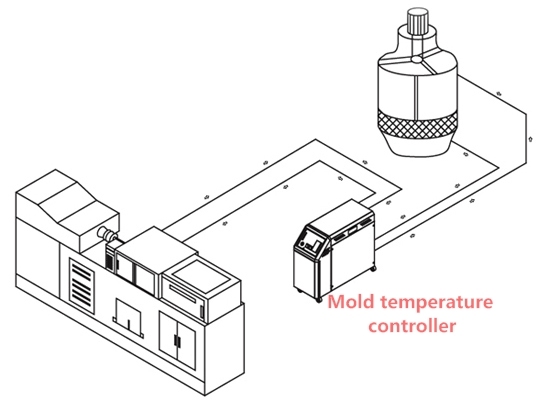
Â
Excavator Cylinder Piston Seals
Precautions for the installation of hydraulic cylinder piston seals in excavators
1. The sealing of the oil cylinder piston should use products of reliable quality to ensure good sealing performance.
2.Before installing the oil cylinder piston seal, the seal and sealing groove should be cleaned to ensure that the sealing surface is free of impurities.
3. When installing the seal, the correct installation sequence and direction should be carried out according to the drawing requirements to ensure the correct installation of the seal.
4.When installing the seal, special tools should be used to avoid using sharp tools and hard objects to damage the seal.
5. When installing the seal, attention should be paid to whether the seal groove is damaged or worn. If so, it should be replaced or repaired in a timely manner.
6. When installing the seal, an appropriate amount of lubricating oil should be applied to avoid friction damage to the seal during installation.
7.When installing the seal, it should be ensured that the compression of the sealing ring meets the requirements to avoid excessive or insufficient compression leading to seal failure.
8.After installing the seal, a sealing test should be conducted to ensure that the sealing performance meets the requirements.
Hydraulic cylinder piston seals, hydraulic cylinder seal, boom seal
Safe Seal Technology Co., Ltd. , https://www.jsspreals.com